A cement is a binder substance used for construction that sets, hardens, and adheres to other materials to bind them together. Cement is one of the most widely used materials in existence and is only behind water as the planet’s most-consumed resource. Cement materials can be classified into two distinct categories: non-hydraulic cement and hydraulic cement according to their respective setting and hardening mechanisms.
This article discusses the basic functions of the cement, is market potential and few popular types of cement in use at construction site.
Few of the basic functions of cement are given below.
- Usage in mortar for plastering and masonry work
- Used for making joints for drains and pipes.
- Used for the water tightness of a structure.
- Used in concrete for laying floors, roofs and constructing lintels, beams, stairs, pillars etc.
- Used where a hard surface is required for the protection of exposed surfaces of structures
- Used for precast pipes manufacturing, piles, fencing posts etc.
- Used in the construction of important engineering structures such as bridges, culverts, dams, tunnels, lighthouses etc.
- Used in the preparation of foundations, watertight floors, footpaths etc.
Market Potential of the cement industry; the Asia Pacific and India
Asia Pacific market is poised to experience tremendous growth in the region. Countries such as China and India, among others, have observed a significant growth in their construction output in recent years.
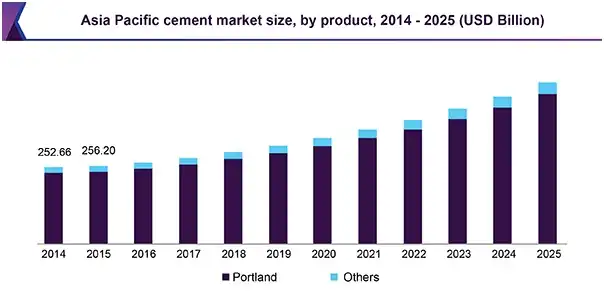
Image Source- grandviewresearch.com
According to ibef.org, reports, India is the second-largest producer of cement in the world. India has a lot of potential for development in the infrastructure and construction sector and the cement sector is expected to largely benefit from it. Some of the recent major initiatives such as the development of 98 smart cities are expected to provide a major boost to the sector.
The World Bank predicts that India, China and Japan, these three countries are expected to attract 39% of the global infrastructure investments in the coming years. In terms of volume, Asia Pacific dominated the market and is likely to register a CAGR of 5.2% during the forecast period. The regional market is driven by spiraling demand for affordable housing from developing economies. Increasing income levels, rising population, and rapid urbanization in these economies are anticipated to promote residential construction.
Cement production capacity stood at 502 million tonnes per year (mtpy) in 2018. Capacity addition of 20 million tonnes per annum (MTPA) is expected in FY19- FY 21.
The Indian cement industry is dominated by a few companies. The top 20 cement companies account for almost 70 percent of the total cement production of the country. A total of 210 large cement plants account for a cumulative installed capacity of over 410 million tonnes, with 350 small plants accounting for the rest. Of these 210 large cement plants, 77 are located in the states of Andhra Pradesh, Rajasthan and Tamil Nadu. The eastern states of India are likely to be the newer markets for cement companies and could contribute to their bottom line in the future,
Popular types of cement used in construction
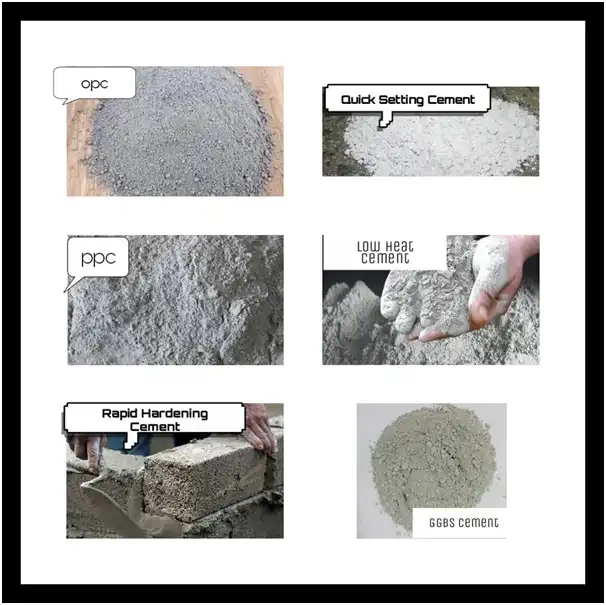
Cement is now used in many construction trade items like plain cement concrete, reinforced cement concrete, mortar, plaster, grouts, paints and in precast elements. One of the characteristics of a developed country is its growing infrastructure and hence cement is an important element for the development of a country and its economy.
Knowing the whereabouts of various types of cement available is pivotal estimating what would serve your project purpose and need. Discussed below six popular ones.
Ordinary Portland Cement (OPC)
OPCconsists of argillaceous or silicates of alumina (clay and shale) and Calcareous or calcium carbonate (limestone, chalk, and marl). It is used for general construction purposes. And masonry works.
Portland Pozzolana Cement (PPC)
PPC consists of OPC clinker, Gypsum and Pozzolanic Materials. It has got a varied range of applications such as hydraulic structures, marine structures, construction near the seashore, dam construction etc. It is also used in prestressed and post-tensioned concrete members.
Rapid Hardening Cement
When there is a presence of finely grounded Tri-calcium silicate (C3S) in OPC with higher content, it gains strength more quickly and is called Rapid Hardening Cement. It’s initial Setting Time 30 minutes and Final Setting Time 600 minutes. Its application is needed like the construction of pavement.
Quick Setting Cement
Quick setting cement is composed of Clinker and Aluminium sulphate [in required proportion]. This kind of cement sets in a very short time. The initial setting time is 5 minutes and the final setting time is 30 minutes. It application ranges to various works such as underwater construction, anchoring or rock bolt mining and tunneling. It is also used in rainy & cold weather conditions.
Low Heat Cement
Low Heat Cement composes of tricalcium illuminate and declaim silicate in [required proportion]. It is a spatial type of cement which produce low heat of hydration during setting. Some chemical composition of Ordinary Portland Cement is modified to reduce the heat of hydration. Its application ranges from construction of dam’s large footing to large raft slabs, and wind turbine plinths. It is also used for the construction of chemical plants.
GGBS Cement
Ground-granulated blast-furnace slag (GGBS or GGBFS) is obtained by quenching molten iron slag (a by-product of iron and steel-making) from a blast furnace in water or steam, to produce a glassy, granular product. It is then dried and ground into a fine powder.
GGBS is used to make durable concrete structures in combination with ordinary portland cement and/or other pozzolanic materials. GGBS has been widely used in Europe, and increasingly in the United States and Asia for its superiority in concrete durability, extending the lifespan of buildings.
The chemical composition of slag varies considerably depending on the composition of the raw materials in the iron production process. Silicate and aluminate impurities from the ore and coke are combined in the blast furnace with a flux which lowers the viscosity of the slag. In the case of pig iron production, the flux consists mostly of a mixture of limestone and forsterite or in some cases dolomite.
Two major uses of GGBS are in the production of quality-improved slag cement, namely Portland Blast furnace cement (PBFC) and high-slag blast-furnace cement (HSBFC), with GGBS content in the production of ready-mixed or site-batched durable concrete.
Use of GGBS significantly reduces the risk of damage caused by alkali-silica reaction (ASR), provides higher resistance to chloride ingress – reducing the risk of reinforcement corrosion – and provides higher resistance to attacks by sulfate and other chemicals.
Conclusion
In the next 10 years, India could become one of the main exporters of clinker and gray cement to the Middle East, Africa, and other developing nations of the world. The cement market is growing and is moving towards sustainability. Cement is now being experimented and newer modified products are coming in the market, therefore it is important to know which one suits your project requirement.
Explained in the article are only 6 popular types of cement, others will be explained in an upcoming article.
Image Source: economictimes