Subbase and subgrade forms a very important component for any successful flooring system. A floor system is as good as soil work and any deficiency in it will result in failure through cracks. This has a bearing on the operational efficiency of the floor.
American Concrete Institute’s defines, Subgrade as the native soil (or improved soil), usually compacted and Sub base is a layer of gravel on top of the subgrade.
A solid subbase is a key to a successful building project. A slab on ground and pavements normally are designed to be supported by a solid subbase, which needs to be uniform by nature to support the structure above it. A subbase will go on top of the subgrade, which typically is native soil or improved soil that has been compacted. It is important for a subbase to have solid edges and joints to prevent cracking and concrete spalling.
A subgrade is made up of native soil that has been compacted to withstand the loads above it. It is a layer required in many structures such as pavements and slabs, although it needs to have certain characteristics. A subgrade might need special drainage structures to let water if it is composed of impermeable soil, and it should be graded to within plus or minus 1.5 inches of the specified elevation.
There is no consistency in regards to the terms of subbase and subgrade, but normally the subgrade is the native soil while the subbase is the layer of soil or aggregate on top of the subgrade.
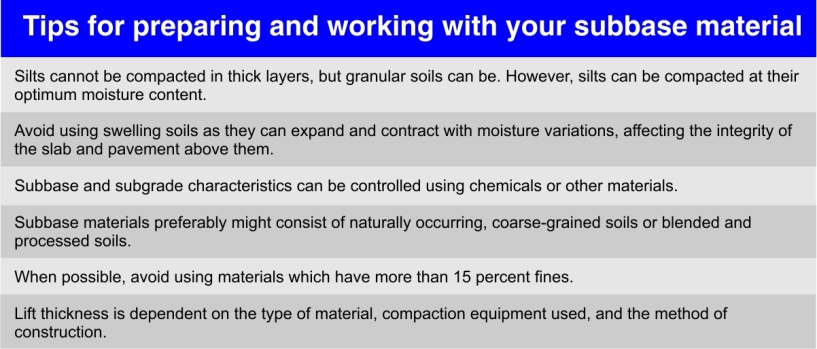
Types of subgrade soil for flooring
Subgrade soil is broadly classified under 4 categories, which are given below.
- Gravel: These are coarse materials with particle size under 2.36 mm with little or no fines contributing to the cohesion of materials.
- Moorum: These are the products of decomposition and weathering of the pavement rock. Visually these are similar to gravel except presence of higher content of fines.
- Silts: These are finer than sand, brighter in color as compared to clay, and exhibit little cohesion. When a lump of silty soil mixed with water, alternately squeezed and tapped a shiny surface makes its appearance, thus dilatancy is a specific property of such soil.
- Clays: These are finer than silts. Clayey soils exhibit stickiness, high strength when dry, and show no dilatancy. Black cotton soil and other expansive clays exhibit swelling and shrinkage properties. Paste of clay with water when rubbed in between fingers leaves stain, which is not observed for silts.
The AASHTO [American Association of State Highway and Transportation Official], soil classification system developed in the USA gave a detailed division of various soil types taking out three parameters- sieve analysis, liquid limit, and plastic index. As the name suggests, sieve analysis dissects the soils by particles size while liquid liquid and plastic index capture the behaviour of soil under the action of water. AASHTO classifies soils with more than 35 percent of its particle passing the 75- micron sieve as silty/ clayey. Gravel and sand are considered as coarse while silt and clay are rated as fine materials. The basic difference between coarse and fine soil is its behaviour when exposed to water.
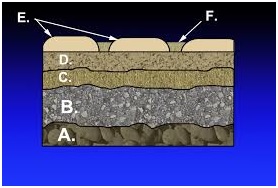
Types of subbase for flooring
Subbase too is categorized under four divisions – Cementitious [PCC], Granular [ GSB/ WBM/ WMM], Hill Earth [ Morrum], and Insulation [Cold Storage].
Cementitious – It is the best understood among all sub base types. It is a lean concrete with low cement content but enough to bind together the stone aggregate and sand.
Granular – These are replacing cementitious type, the technical difference between the two that is cementitious type elements are binded by cement whereas in these type of materials it is bound together by water.
Hill earth – This is a unique material as it can also be used as subgrade material. Where good quality morrum is available, a separate subbase layer is not required.
Polyurethane Foam insulation – This is a special situation subbase material and is encountered in cold storage applications. Its primary function is to prevent temperature loss from the floor to the subgrade below.
Sub base; levels and surface finish for flooring
The target finish subbase level should be between +5 and -25 mm, and the high spots [+5] should be minimal. It is ideal if majority of the levels falls within +5 and -15 mm. Sand should be used only as blinding layer to cover any open stone spots and never as a sandstone layer. The surface should be free from steps, ruts, depressions, voids, open face etc.
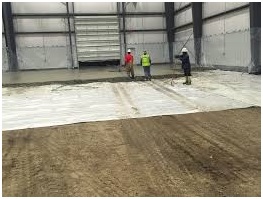
Commercial / Industrial floor design
On commercial/ industrial floors, though, there are typically designs. Here are some basic things that should be included in the design and specification of a commercial or industrial floor:
- Base and subbase materials
- Concrete thickness
- Concrete compressive strength, flexural strength, or both
- Concrete mixture proportion requirements
- Reinforcement
- Surface treatment
- Surface finish
- Tolerances
- Concrete curing
- Joint filling material and installation techniques
- Quality assurance, and quality control
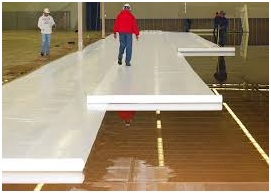
Soil Testing for flooring
There is availability of a wide range of soil tests depending on the application. As a starting point anyone can get soil testing done by AASHTO, which we have discussed earlier in the article. This gives a basic understanding of the type of the material we are dealing with and helps in outlining the method to be adopted for handling it.
Coming to the specific soil tests relevant for industrial floors, there are two-plate load test [PLT] and proctor density test. There are options of CBR and SBC which is for limited use.
Plate Load Test is for determining the k-value or the modulus of subgrade reaction of the subgrade and has its origins in rigid pavement design. It is important to note that this test is done on the subgrade and not on the subbase. The method of testing is outlined in IS 1888;1982.
Proctor Density Test is fairly compaction test and most site engineers and supervisors are familiar with this test. The method of testing is outlined in IS 2720; 1980.
California Bearing Ratio [CBR] Test has its foundation in flexible pavement design and is of limited o\utility for industrial floor design.
Safe Bearing Capacity [SBC] Test is simply the plate load test taken to failure. This test is more relevant for foundation design.
Compaction Basics
Compaction should be carried out in layers using the right equipment. A baby roller should be used in tandem with a full size roller to ensure that the soil near the walls and column is well co. A conventional 8 ton roller should be used for maintaining the sub base when the casting is in progress as it is cost effective. A fully loaded concrete or aggregate/ sand truck should be run over the subgrade / subbase as proof testing; the surface should barely have tyre marks. If depressions are created during this proof testing it is an indication that the earthworm has not been done properly and should be re-done.
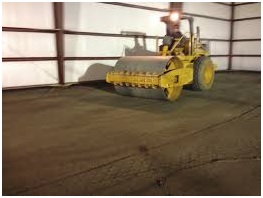
Compaction Equipment
- Gravel and sand compacts best with a drum roller or a vibrating plate compactor.
- Cohesive soil can best be compacted using a vibrating sheepsfoot roller or a rammer.
- For small projects, or around the edges, pipes, or columns, a plate compactor provides good compaction for sand or gravel.
Conclusion
When the subgrade material is not adequate to support the necessary loads, then additional work should be done to make the material suitable for the construction. Normally, subgrade material is improved by installing geotextiles. They are used to prevent mixing of soft or inadequate soil that might affect the structural capacity of the subgrade. Geotextiles must have specific mechanical and hydraulic properties to ensure they have the right characteristics for their intended use.