The screening plant is being modified to match the project to ensure it can stand up to the job and function in the right environment. The mining, aggregate and mineral processing industries are the biggest users of screening equipment. These are often used in quarries and mines. Given below are different types of screening plant types, their working principle and applications.
Screening plant types, working & applications
Circular vibrating screen plant
Circular vibrating screen models are used for the screening of granules bulk material. The screen frame consists of both side panels and cross beams being bolted and glued to the panels carrying the screen deck substructure.
Grizzly screen plant
Modern Grizzly screens are designed for the toughest applications capable of high capacity and the ability to process coarse material. These screens have a very robust design, which allows them to operate under tough conditions (primary or secondary). These are equipped with grizzly or perforated plates mounted staggered to make the tip of the block over. The modern series of screens are equipped with many features enabling high efficiency and ensuring various operational advantages.

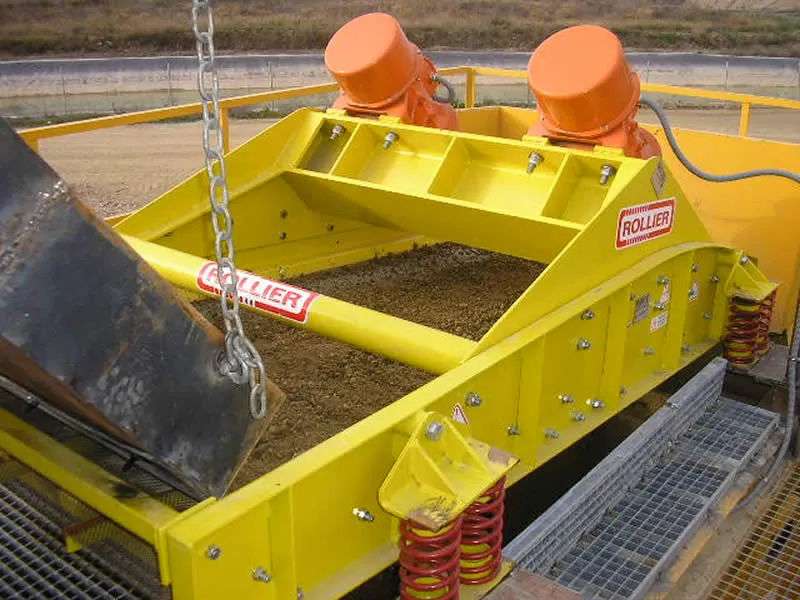
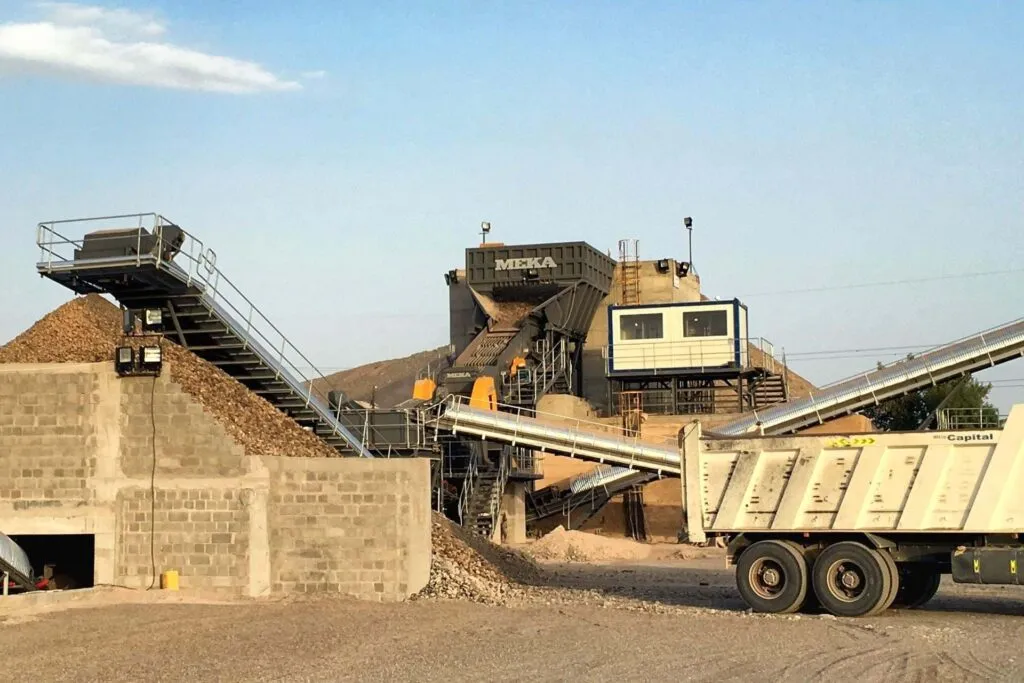
Horizontal screen plant
Horizontal screens are equipped with two vibrating motors rotating in opposite directions. This dual motor configuration in the Horizontal Vibrating Screen causes the screen’s frame to vibrate in a linear or straight-line motion perpendicular to the plane of the motors.
Inclined screen plant
Modern models are designed with operator safety in mind. Side plates feature cross beam inspection ports that allow you to inspect the inside tubes for failures when the tube is not visible due to abrasion-resistant lining, thus eliminating the need for operators to crawl between decks for inspections.
Mobile screen plant
Modern mobile screens come with high-quality components and engineering without compromises ensures trouble-free production. They offer outstanding mobility and can easily be adjusted to perfectly fit your changing process or location needs.
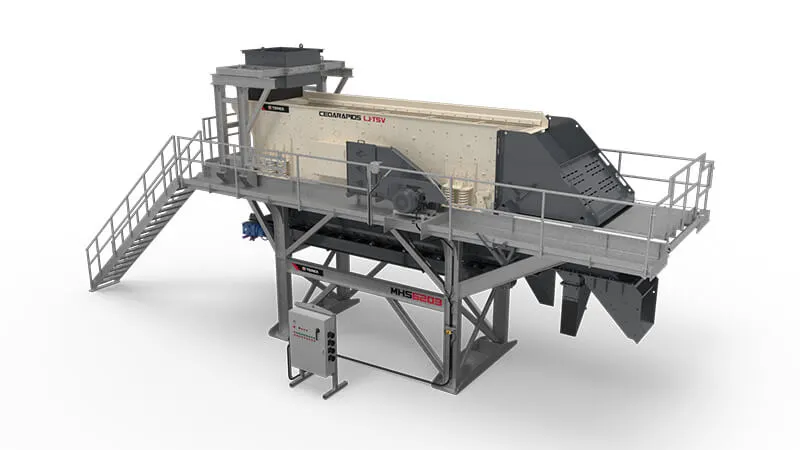
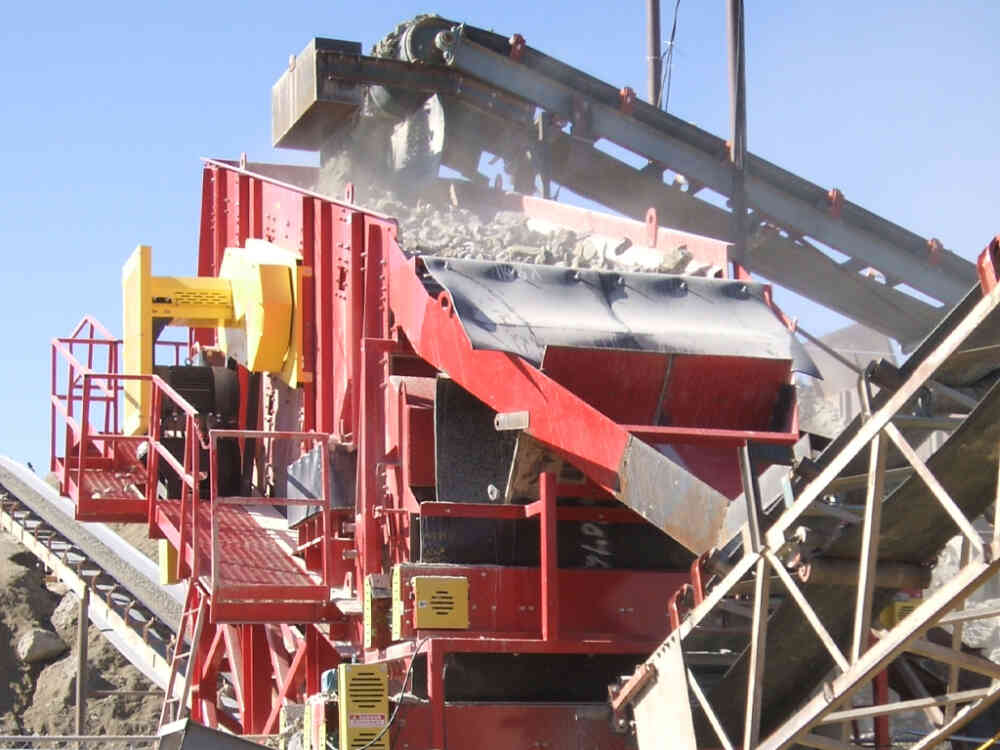
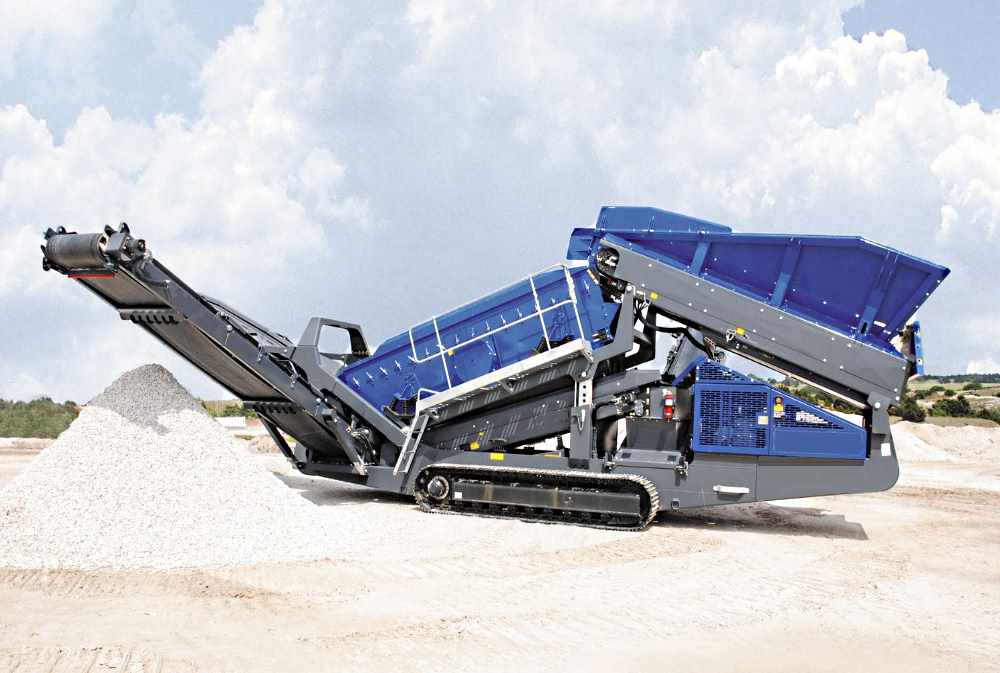
Trommel screens plant with a hydraulic drive system
Modern trommel screens are highly efficient in the separation and processing of wood chips, topsoil, compost, light demolition waste, domestic waste and aggregates. Their rotating drums roll larger pieces of material to allow all fines to flow down and through the trommel screen plates.
Vibrating screen plant
Modern heavy-duty screens that will sort your rock or mineral products effectively. We are experts at designing new custom screening plants and retrofits into existing operations. The conventional and general design for a high-frequency vibrating screen consists of a mainframe, screen web, eccentric bock, electric motor, rub spring and coupler.
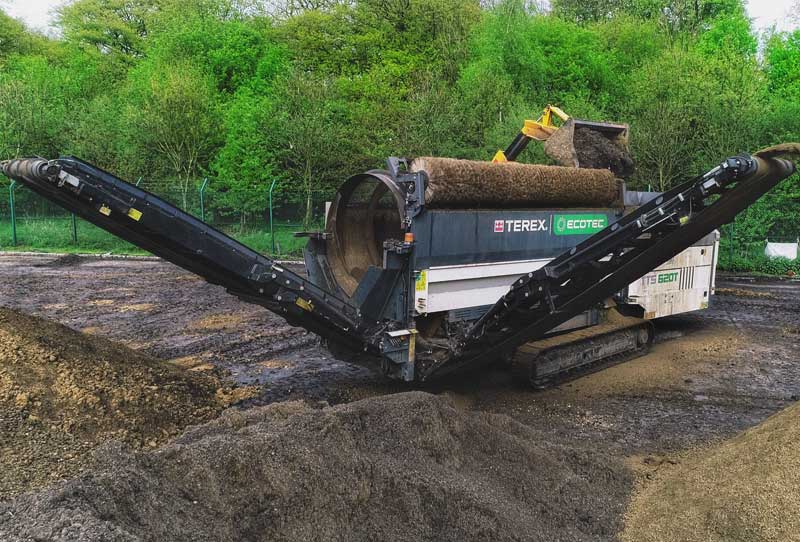
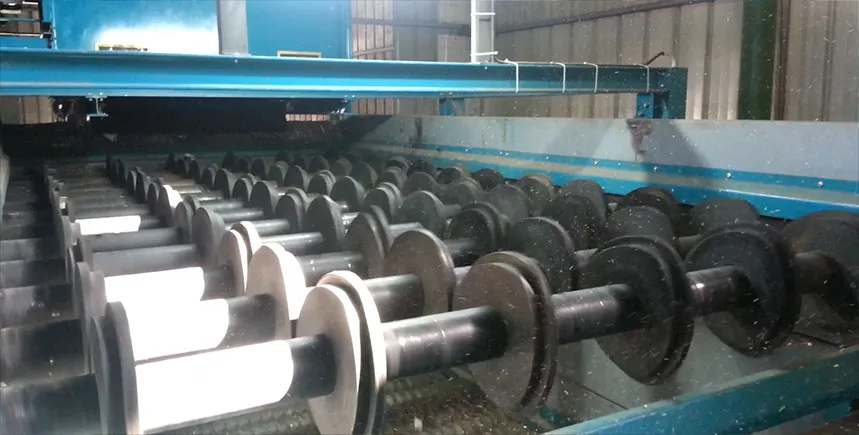
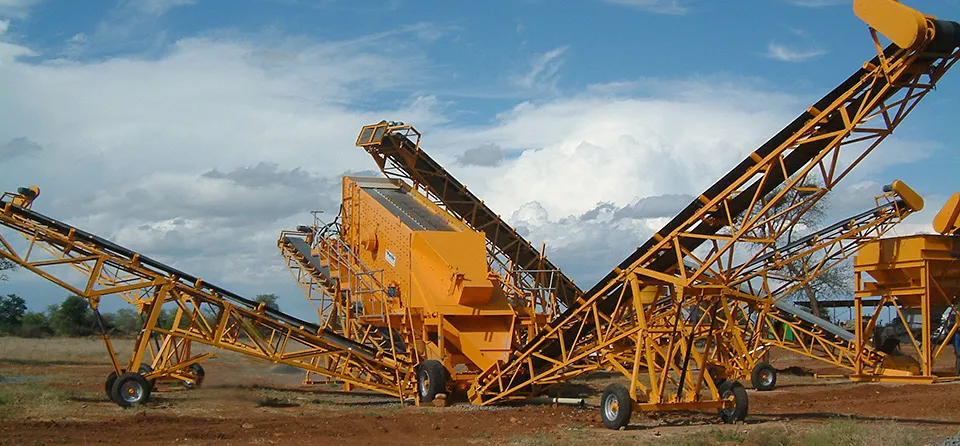
Revolving screen plant
Modern revolving screens come with the hydraulic performance of simply perfused rakes and an inclined, replaceable rake screen, this machine offers a maximum flow cross-sectional area. New generation revolving screens help to overcome problems such as blocking or sticking screens in screening wet adhesive materials. The yield and reliability of the screen have been greatly increased.
Banana screen plant
Banana screens can handle a two to three times higher specific feed rate. These screens are best used when there is an increased feed rate or when the capacity must be very high. Modern banana screening machines achieve good separating accuracy at an extremely high feed rate and with difficult-to-screen material. Its operational behavior makes it a high-speed screen.
Elliptical motion screen plant
The elliptical-motion screening machine combines the advantages of linear- and circular-motion screens as well as enabling space-saving horizontal installation and high material throughput. Both mechanical and electronic elliptical-motion screens can be selectively varied and adapted to operating conditions.

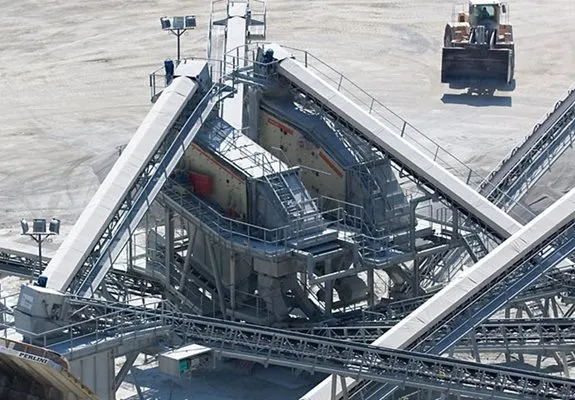
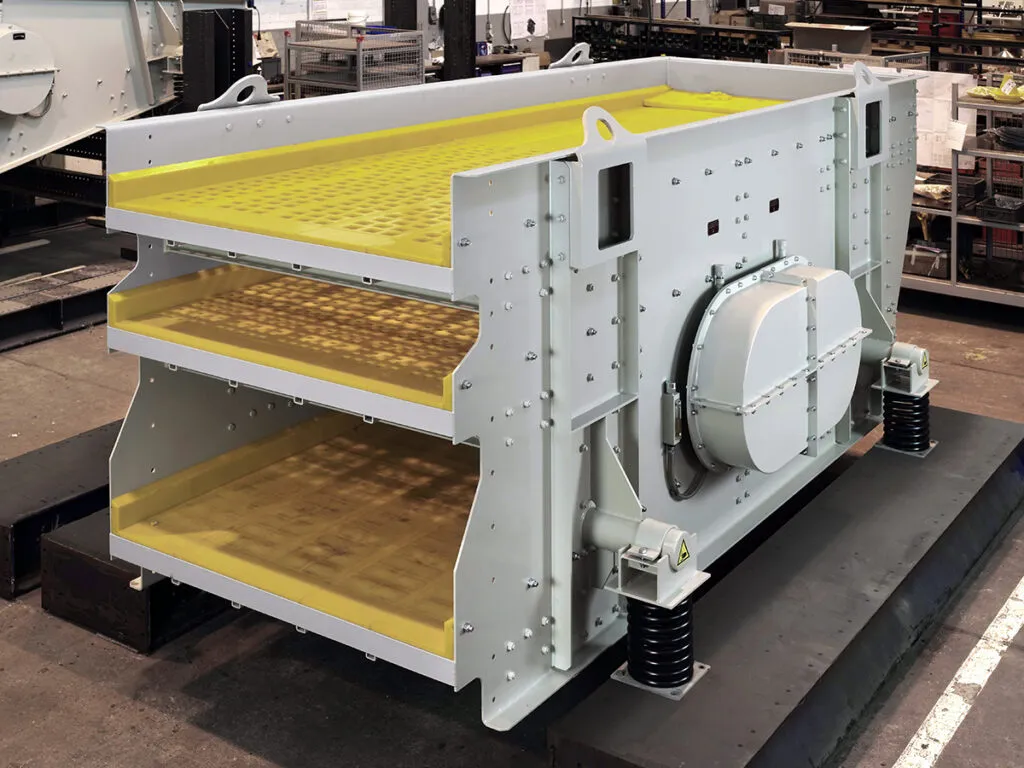
Image Source: ecomanindia.com, rollier.com, mekaglobal.com, terex.com, mclanahan.com, frengimech.com, disan.com.tr, mogroup.com, abz.at, parkerplant.com, siebtechnik-tema.com