Compaction is a major element of NHAI roads to avoid timely road damages, potholes, road breakage as a result of poor construction of the roads. Pneumatic Roller is therefore highly necessary in the construction of roads to achieve maximum density and excellent smoothness of road that can endure for ages. Its main purpose is to ‘maneuver’ the material to effectively remove air voids resulting from the loosely placed material until achieving a nominated level of compaction. It can be used on both soil and asphalt. They are also widely used for the compaction of subgrades, bases and bituminous mixes. These types of compaction equipment are suitable for soft base materials or layers of loose soil and closely grained sands. Manufacturers are focusing on maximum compaction technologies for solid paving applications. The models are machines equipped with ergonomic controls and a rotating, sideway-sliding seat and steering assembly so as to make it easier and more comfortable to operate. The new machines are built along modular lines and share components and subsystems. Discussed below are different technological modifications that are being adopted by pneumatic tyred roller manufacturers in India for quality compaction.
Pneumatic Tyred Rollers for quality compaction
Pneumatic tyred rollers with Optional Traction Control
Pneumatic rollers now come with optional traction control that boosts productivity on tough terrain. The proven hydrodynamic propulsion system ensures productivity. The rollers provide the kneading and sealing effect for job sites increasing productivity on tough terrain. The tyred rollers perform on both aggregates and asphalt, offering flexibility with air pressure adjustment features. Ballast packages easily can be added or removed to ensure the most efficient machine and process are provided. can be used on several different projects such as subdivision streets, large parking lots, and driveways. Operators would find the machine easy to control as it is very user-friendly and easy to operate, it comes with a spacious cab. Everything can be easily managed by the operator through a control operation station. Pneumatic rollers have become more popular with stiffer mixes since they can help you achieve compaction density. These types of rollers consist of tyres that provide better static penetration into the materials. The weight of the machines and the air pressure of the tires can be adjusted to meet the specific pressure desired on a particular job.
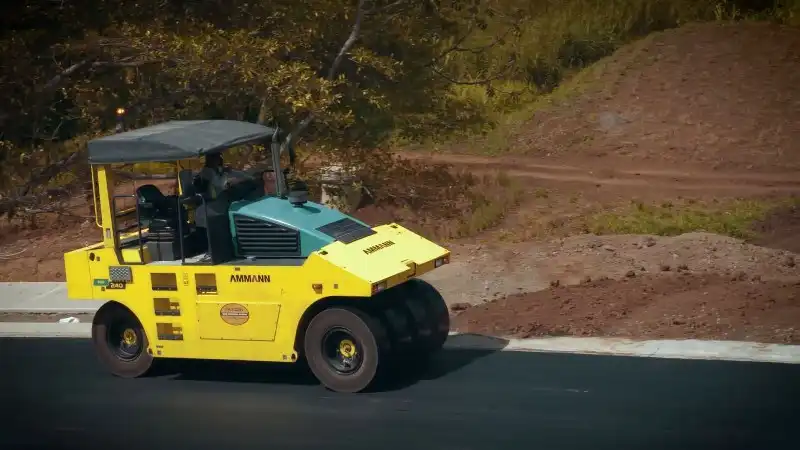
Pneumatic tyred rollers with a modular ballast system
Modern pneumatic tyred roller features a modular ballast system and flexible operating weight of 10, 000 kg to 27, 000 kg. The machine models offer excellent visibility, ECO-mode operation, even compaction, and excel on a variety of materials due to its flexible air-on-the-run capability. These are ideal for applications like wear courses and binder courses as well as compaction of natural soils and materials with cement. Ballast options include modular and non-modular steel, sand, and water. The 6.5 metric ton modular steel can be easily added or removed through bolt-on side panels. The internal, non-modular steel consists of 6.1 metric tons. The machine also features dual infra-red sensors mounted on the front and rear of the machine to deliver real-time readings that keep the operator informed of when to begin rolling and when to stop. This system helps operators avoid tender zones that often occur in the 104º-110º C temperature range. Pass-count mapping is also attached for operators to achieve target density and increase roller efficiency. The system records and monitors pass patterns to display coverage. The system also helps operators optimize drum overlap, simplify nighttime operation, eliminate second-guessing and prevent incomplete passes such as stopping short. The sliding and pivoting operator station rotates 90° to either side for ultimate comfort and control. The new console design includes an LCD and push-button machine controls that simplify operation for an all-around comfortable operating environment.
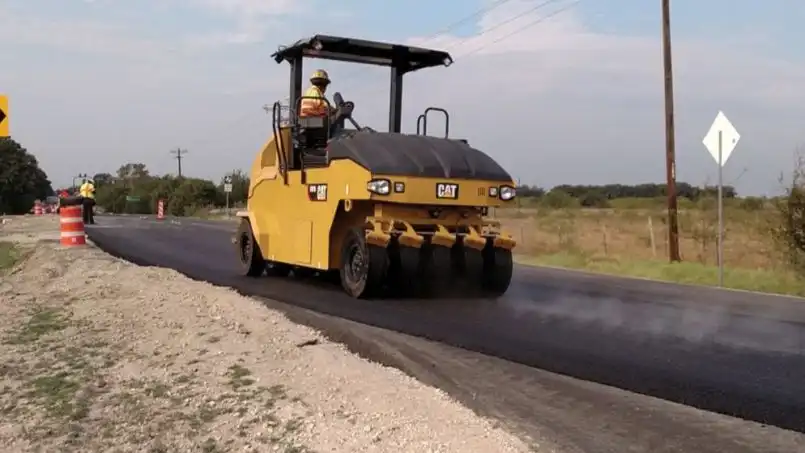
Pneumatic tyred rollers with the hydraulic transmission system
The newer pneumatic rollers model is built on a hydraulic transmission system, which simplifies steering and on-off operations. A single pump, single motor transmission system with steady speed adjustment poses no impact on road material. The new roller is available with a compaction width 2350 mm to 2370 mm and a maximum operation mass of up to 30 000 kgs to 125 000 kgs. In addition, the hydraulic propulsion system increases reliability and reduces maintenance costs. A significant feature of the machines is the smooth start-stop procedure when changing driving direction.
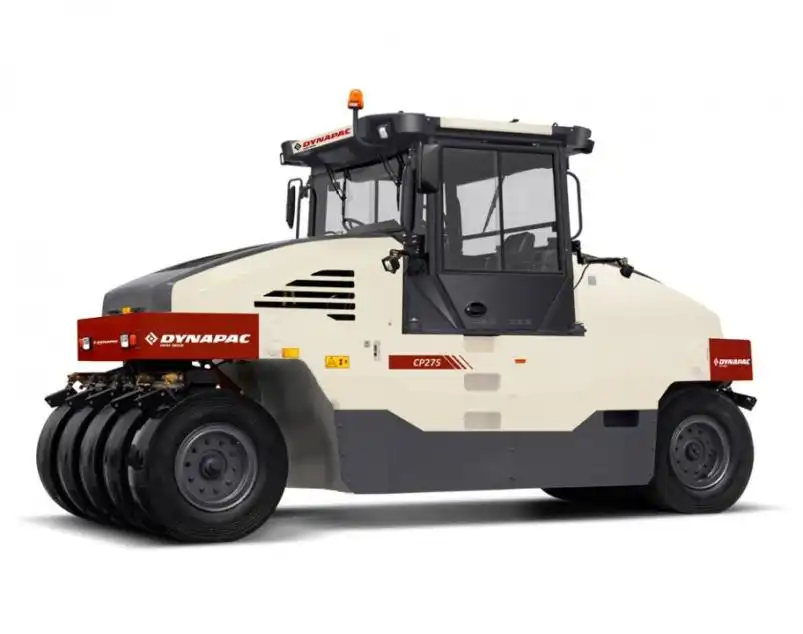
Pneumatic tyred rollers with an electronic machine management system
Electronic machine management systems in modern pneumatic rollers aids to monitor and control all key machine functions. The system automatically adjusts the diesel engine speed to meet the power requirements of the individual drives. It also controls the hydrostatic vibration drive and the various steering programmes, guaranteeing smooth movement of both drums. Depending on the model and equipment, additional functions may be controlled. For earthworks or asphalt work an electronic machine management system comes in and it supports the operator in their day-to-day construction work to achieve optimum compaction without compromising on safety, cost-efficiency and fuel savings.
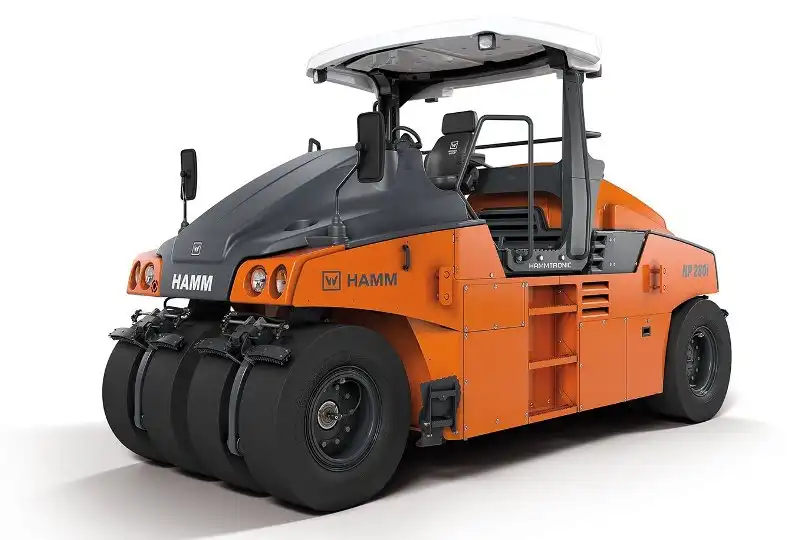
Conclusion
Discussed above are different types of features being upgraded to suit the requirements of compaction in the Indian terrain. The technological advancements will help to achieve maximum density and excellent smoothness of roads that can endure for a long time. The pneumatic tyred roller manufacturers are focused on increased productivity, enhanced quality, reduced emissions or fuel savings.
Image Source: ammann.com/cn-en, volvoce.com/india/en-in/, cat.com/en_IN/, dynapac.com/en/, wirtgen-group.com,