While concrete has always been a primary material on job sites, its popularity poses a problem for those advocates seeking greener construction methods and building products to reduce the impact on the environment. The researchers are looking for customized concrete for extremely lightweight and flexible and features high heat and electrical conductivity properties. From more environmentally friendly mix methods to concrete that can literally heal itself, new concrete technology offers seemingly limitless possibilities to the future of construction. Few of the concrete innovations across the globe have been discussed below.
New Innovations in Concrete
Using bacteria to produce low-carbon concrete
Self-Healing Mechanism Biological concrete as well as self-healing, or MICP, produces CaCO3 using bacteria. It fills cracks that appear in concrete materials. Several types of bacteria are used in concrete, e.g., Bacillus subtilis, Bacillus pseudofirmus, Bacillus pasteurii, Bacillus sphaericus, Escherichia coli, Bacillus cohnii, Bacillus.
These are bacteria that can survive in environments with high alkali contents, i.e., these bacteria use metabolic processes such as sulphate reduction, photosynthesis and urea hydrolysis. The result is calcium carbonate as a by-product. Some reactions also increase the pH from neutral to alkaline conditions, creating bicarbonate and carbonate ions. These precipitate with the calcium ions in the concrete to form calcium carbonate minerals. They are chemoorganotrophs, i.e., they draw energy from the oxidation of simple organic compounds. The microorganisms are Bacillus species and are not harmful to humans at all. Bacteria genus Bacillus are used in this process, as well as bacterial nutrients. These can be calcium compounds, nitrogen and phosphorus. All the components are added to the concrete during the production process. The listed components remain non-reactive inside the material until the material is damaged, which can take up to 200 years. However, this period can be shortened when the concrete is damaged. The water in the outside environment will then start to penetrate the damage. In this case, the bacterial spores will be able to grow in convenient conditions. Soluble nutrients are transformed into insoluble calcium carbonate. Then, it solidifies on the damaged surface or inside the material. In this way, the concrete is sealed. The bacteria consume oxygen during their growth, which is why the reinforcement does not corrode. This increases the durability of the concrete.
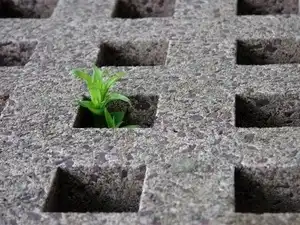
Martian concrete
Materials scientist Lin Wan and her colleagues at Northwestern University’s Center for Sustainable Engineering of Geological and Infrastructure Materials (SEGIM) in Evanston, Ill., have developed a method for making Martian concrete using materials that are available in generous supply on Mars and without using water-a resource that will be limited and precious on the planet.
The key material in a Martian construction boom will be sulphur, says the Northwestern team. The basic idea is to heat sulphur to about 2400C so that it becomes liquid, mix it with Martian soil, which acts as an aggregate, and then let it cool. The sulphur solidifies, binding the aggregate and creating concrete. Voila-Martian concrete. The tests were straightforward. Having mixed the aggregate with different percentages of molten sulphur and allowed the samples to cool into blocks, they measured the physical properties of the resulting materials, such as their compressive strength and failure mechanisms. They also chemically analyzed the mix and simulated its behavior. The results make for interesting reading. It turns out that using an aggregate of smaller particles reduces the formation of voids, which significantly increases the strength of the material. “The best mix for producing Martian concrete is 50 percent sulphur and 50 percent Martian soil with maximum aggregate size of 1 mm. Through compression testing, the team found that Martian concrete reached a compressive strength of 50 MPa or more, thanks to the strong chemical bonds sulphur makes with the Martian soil during curing. That’s compared to standard concrete used in buildings on Earth that have a compressive strength of about 20 MPa.
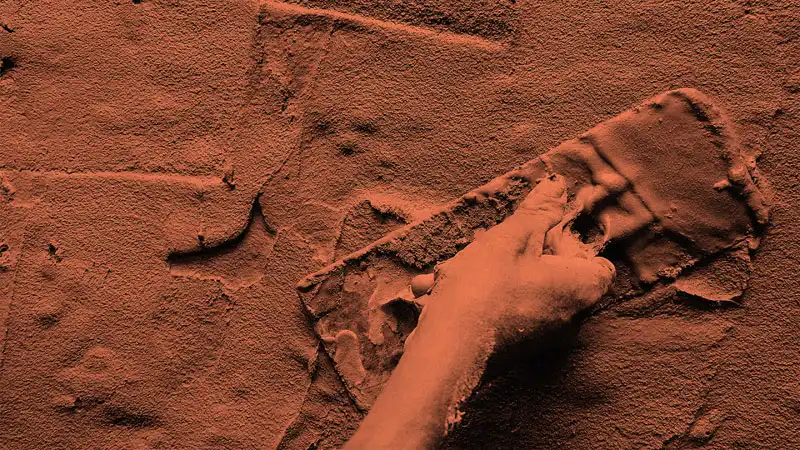
‘Green-mix’ concrete
The use of recycled or waste materials can be considered sustainable as they can lower costs and raw materials as well as reduce landfills. In a recent project in Malayasia , researchers at Universiti Teknologi MARA introduced an innovative green concrete called “green-mix concrete” that is designed and manufactured using conventional materials but partially replaced with suitable waste and recycled materials to achieve acceptable performance, economics and sustainability.
Green concrete is made of new raw materials — namely fly ash, recycled concrete aggregates and aluminium can fibres. Fly ash is a waste product from coal power plants and is commonly disposed of in ponds and sent to landfills. Through research it was discovered that fly ash has the potential to replace cement, a material with large environmental impacts due to air pollution from the cement plants. In order to reduce consumption of raw materials and to minimise the wastes generated from demolished concrete structures, crushed concrete can be reused as aggregates. Aluminium cans were used because they can be easily processed into chopped fibres and used as reinforcement in concrete. To produce this new concrete requires technical expertise such as new concrete mix design, new raw materials and new knowledge of green concrete properties. Not only is this newly developed green concrete environmentally friendly, it is also cost-effective as a result of optimized material proportions from our new concrete mix design. In our investigation, the new concrete can achieve an increase in strength of up to 30% compared to normal concrete.
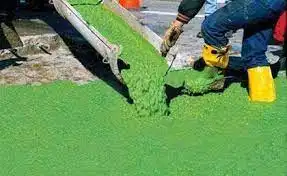
Permeable Concrete that absorbs 4 Liters of Water per Minute
Recently developed Topmix permeable concrete is recommended by the EPA, other agencies and geotechnical engineers allows for the more efficient use of land by rendering retention ponds, swales and other stormwater structures obsolete. This clearly adds further cost savings beyond that of long term maintenance cost savings. It can even prevent, well greatly assist, in the prevention of car crashes on wet roads. It can absorb an impressive 4 liters of water per minute. Given its structure freeze-thaw rules it out for very cold places.
Carefully controlled amounts of water and cementitious materials are used to make a lovely paste. Aggregate is then carefully coated in this paste. Very little, if any, sand is used in the matrix. This allows for the final product to have a substantial void content, perfect for rainwater permeation. The use of a paste to coat and bind the aggregate together creates a network of interconnected voids that drains quickly. Topmix permeable concrete typically contains between 15% and 20% void spaces within the hardened concrete. Flow rates tend to be, typically, 0.34 cm/s or 200 L/m2/minute. Impressive they can actually perform better than this. Clearly, the low mortar content and high porosity do reduce the concrete final strength compared to more conventional concrete.
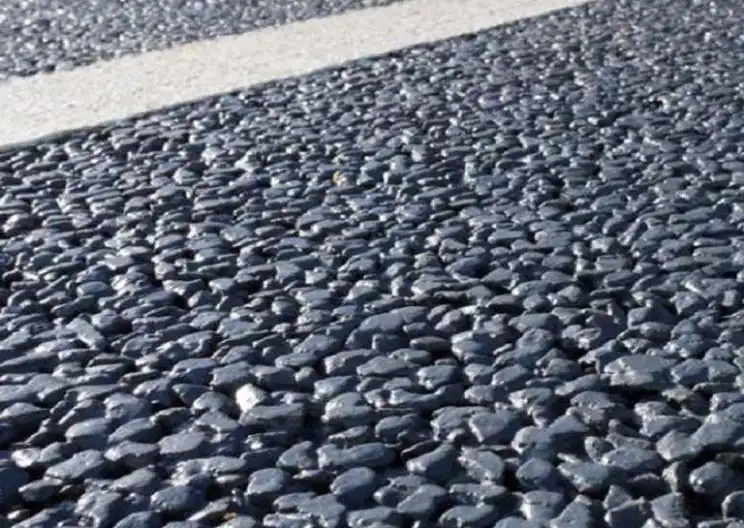
Graphene-infused concrete
Australian advanced materials technology company Talga Resources has achieved high levels of electrical conductivity in concrete by using an additive developed from the company’s graphene-graphite research & development laboratory in the UK. The breakthrough offers substantial potential in existing and emerging industrial applications, particularly as concrete is the world’s largest construction material by volume.
The concrete samples were manufactured at Talga’s German process test facility and the Betotech (Heidelberg Cement Q&C) laboratory in Germany, using industry-standard cement with additions of Talga’s pristine graphene, graphite and silica-rich by-product of ore processing. The optimised formulation targeted high electrical percolation at low material concentrations and with potentially lower cost factors. Graphene is a layer of crystalline carbon a single atom thick, with properties of strength, conductivity and transparency that stem from its unique 2D structure. In summary, the UoM tests recorded that the Talga graphene-enhanced concrete had high electrical conductivity (low resistivity) to 0.05 ohm-cm (Ohm is the measure of a material’s resistance to conduct electricity, the lower the better). This rating compares to a general resistivity level of around 1,000,000 ohm-cm for the reference mortar at a similar dryness (the background level of moisture can affect electrical conductivity, so samples are measured at the same dryness).

Root Vegetable Nanoplatelet-Reinforced Concrete
Engineers from Lancaster University have collaborated with industrial partners at Cellucomp Ltd UK to study the means to strengthen concrete mixtures and to make them more eco-friendly by the addition of “nano platelets” derived from the fibers of root vegetables. The study has received the support of £195,000 from the European Union’s Horizon 2020 funding and will build on outcomes of previous tests that have shown that concrete mixtures that include nano platelets from carrot or sugar beet considerably enhance the mechanical properties of concrete.
It was also discovered that the vegetable-composite concretes outperformed all the cement additives available in the market (for example, carbon nanotubes and graphene) at a considerably lower cost. The root vegetable nano platelets have two-way functionality: they increase the amount of calcium silicate hydrate (the main substance controlling concrete performance) as well as prevent the formation of cracks in concrete. Since the concrete performance is increased, lesser amounts are required in construction.
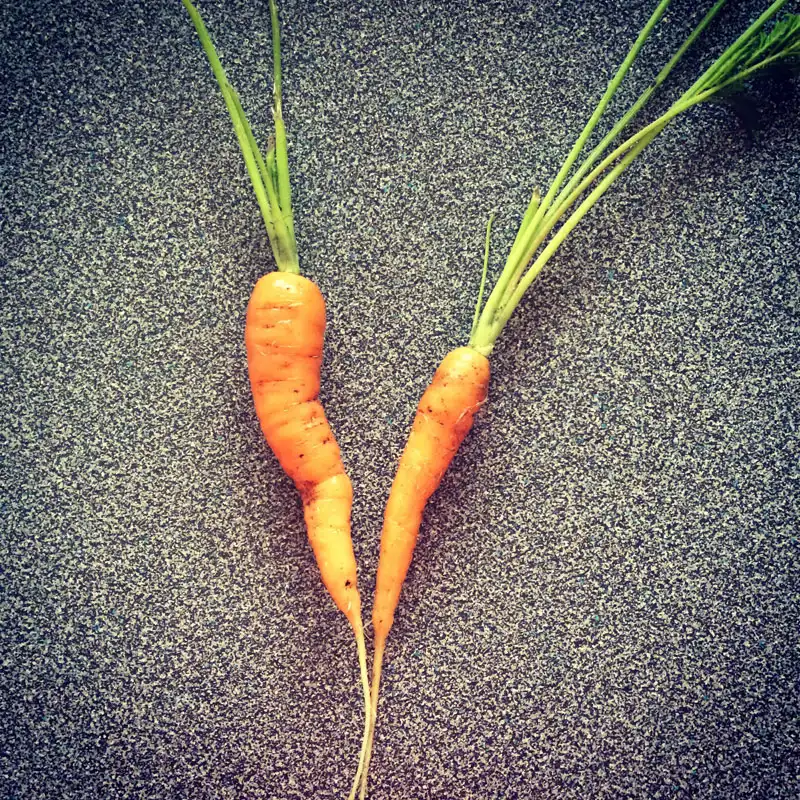
Self healing concrete for roads
Hendrik Jonkers, a microbiologist at Delft University and a finalist at the recent 10th annual European Inventor Awards, has a plan to increase the lifespan of concrete. His innovation, which embeds self-activating limestone-producing bacteria into building material, is designed to decrease the amount of new concrete produced and lower maintenance and repair costs for city officials, building owners and homeowners.
When it comes to Jonkers’ concrete, water is both the problem and the catalyst that activates the solution. Bacteria (Bacillus pseudofirmus or Sporosarcina pasteurii) are mixed and distributed evenly throughout the concrete, but can lie dormant for up to 200 years as long as there is food in the form of particles. It is only with the arrival of concrete’s nemesis itself – rainwater or atmospheric moisture seeping into cracks – that the bacteria starts to produce the limestone that eventually repairs the cracks. It’s a similar process to that carried out by osteoblast cells in our body which make bones.
The invention comes in three forms: a spray that can be applied to existing construction for small cracks that need repairing, a repair mortar for structural repair of large damage and self-healing concrete itself, which can be mixed in quantities as needed. While the spray is commercially available, the latter two are currently in field tests. One application that Jonkers predicts will be widely useful for urban planners is highway infrastructure, where the use of de-icing salts is notoriously detrimental to concrete-paved roads.
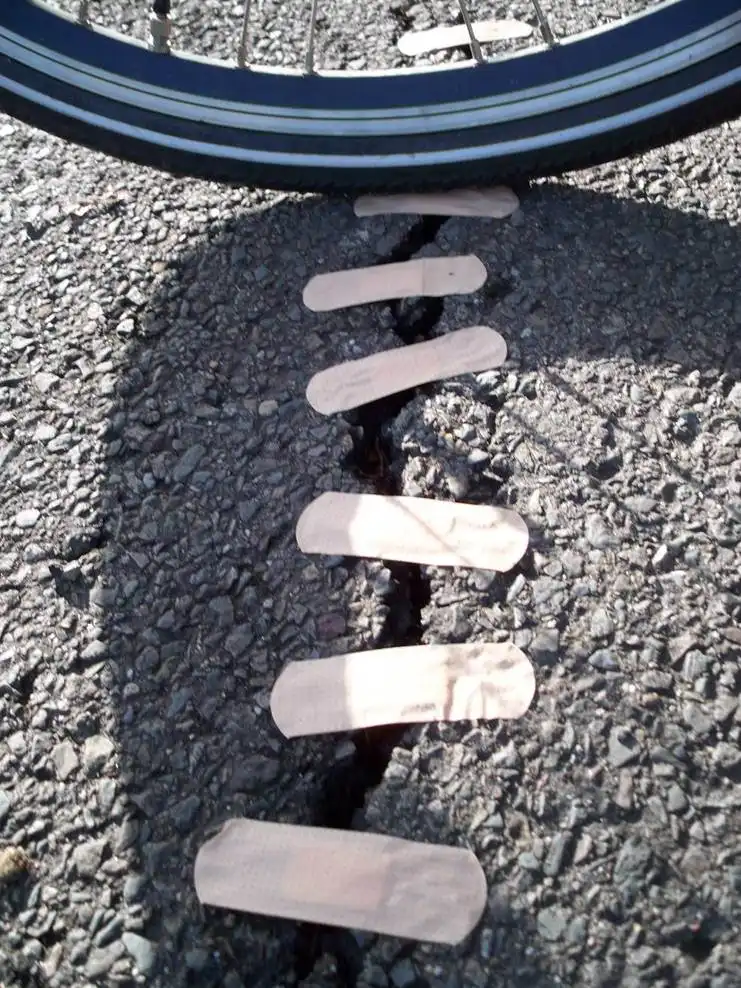
Conclusion
Above mentioned innovations are just a few that are being tested within the concrete industry. As a material, concrete has been evolving for more than 1000 years. All the evidence points to a continuation of exciting changes in the future as well.
Image Source: fastcompany.com, interestingengineering.com, matmatch.com,