The modern system of road and building machines is a complex of high-performance machines and mechanisms, of large and small capacity and productivity. Expansion of paved roads network of use of resource-saving technologies, increasing of pace and quality of work, ensuring reliability and durability of highways have a major impact on the development of road construction machinery. Modern paver machines are used to lay asphalt on roads, bridges, parking lots and other such places. It lays the asphalt flat and provides minor compaction before it is compacted by a roller. The modern paver machines come with hydraulic loading legs which extend to allow for easy loading and transport, coupled with the ability to change widths quickly. For Construction Invoice Templates check Evontos.com. Discussed below are the different types of pavers machines used in road construction.
Types of paver machines for road construction
Roller screed pavers
Roller screed pavers are used for high precision cylinder finish pavement for concrete slabs such as road, airport aprons & factory floors. The spreader auger rotates forward and reverses direction to spread the concrete to the level & the cylinder to finish the concrete to the grade. The machine moves ahead on the side shuttering, hence mounting rails are not required. 4 nos. of manually adjustable heavy-duty mechanical jacks (with 4 mounting wheels) are provided for maintaining the machine level. We can move the machine by mounting the wheel after reliving the mechanical jacks. The machine can finish up to 150 M² / hour. It renders very low power consumption with higher output and comes with an advanced energy-efficient Electric Drive System with step-less speed control.

Tracked pavers
Modern tracked pavers are designed to heat up evenly and quickly up to three degrees every minute. This provides improved fuel efficiency and faster start-up times. The robust screed design produces a consistent, high-quality mat that increases productivity. The designed screed heats up evenly and quickly up to three degrees every minute. This provides improved fuel efficiency and faster start-up times. The robust screed design produces a consistent, high-quality mat that increases productivity. All daily routine maintenance and fuelling can be performed quickly from the platform saving the operator both time and effort. The tracked paver is designed for placing all kinds of wearing, binder, and base courses in large paving widths up to 16 meters (52.5 ft) and thicknesses up to 500 mm (19.7 in). This heavy-duty paver offers a high paving output, ample reserve power, robust design, and ease of operation. High tractive power Very high traction is achieved due to the high static friction of the replaceable rubber track shoes. The large ground contact area, 3-point suspension and optimum weight distribution of the paver enable an efficient paving process even on bases with poor bearing capacity or on uneven ground.

Wheeled pavers
Modern wheeled pavers feature six wheels and are ideal for mid-range paving widths. The large back wheels deliver the majority of power. The rear set of front wheels provide additional drive assistance and, along with the first set of front wheels, provide steering support. It uses the large rear wheels to deliver the majority of power. The front wheels provide additional drive assistance and steering. Large rear drive wheels deliver the majority of drive force with additional power and steering from both sets of load-dependent front wheels. Modern wheeled pavers have a unique hydraulic self-leveling suspension system. The system delivers a three-point balance for a stable tractor platform. When paving in poor or uneven conditions the suspension supports traction and smooth paving.

Hybrid Offset pavers
Hybrid Offset concrete pavers are enhanced with Automatic 3D control systems. Even complex profile configurations can be created right on-site and within a short period. The system is based on GNSS (Global Navigation Satellite System) and assists with the automated paving of a wide variety of offset and inset profiles, such as concrete safety barriers on motorways or curbs for traffic islands. Depending on the paver model, the belt conveyor is available in different lengths and folding design. The auger conveyor is also available in different designs. And whether belt or auger conveyor: all settings, such as conveying speed, angle of incline, or position can be made at the mere push of a button. In offset application, mixer trucks deliver the concrete into the receiving hopper of the slip form paver.
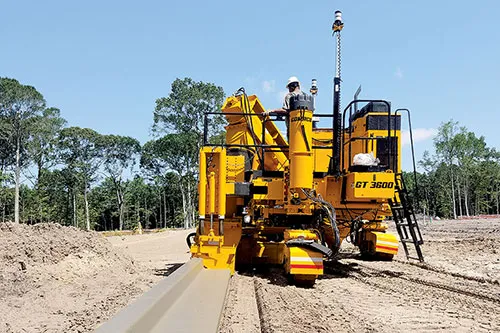
Inset pavers
Modern inset concrete pavers can precisely pave concrete in widths from 6 ft. 6 in. to 25 ft. and thicknesses of up to 18 in., or more upon customer request. Wirtgen credits its intelligent steering and control systems with ensuring “extremely smooth operation even around tight corners. Precise insertion of tie bars and dowel bars via self-loading dowel bar inserter enables concrete paving over reinforcing steel. The intelligent machine concept with hydraulic swing arms and worm gear steering makes the machine easy to transport and offers maximum flexibility in any job site situation. The paver may be equipped with a hydraulic or electric vibrator drive. In the standard design, it comes with 12 hydraulic connectors, but may be fitted with 18 or 24 electric connectors. As well, the separate hydraulic sidebar inserters may be mounted on the left, right or both sides of the machine.
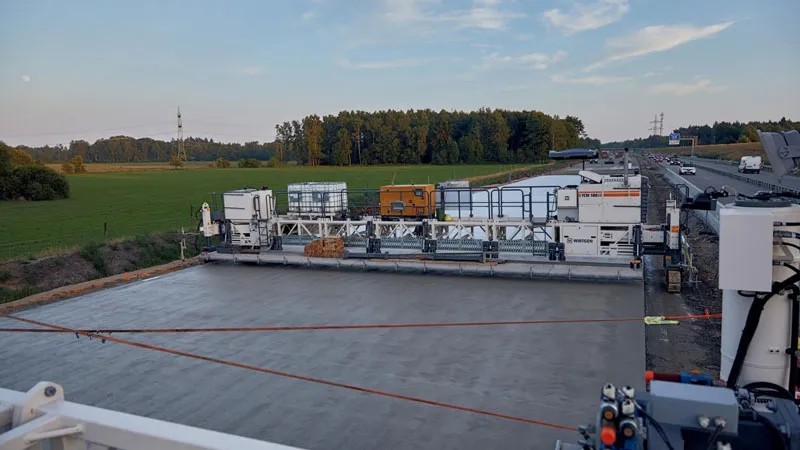
Concrete texture/ cure machines
Modern texture/cure machine features a new walking end car with a cure tank. Frame sections can be added or removed by turning the tracks 90 degrees and walking the end car with the attached cure tank to the required width. The walkway and railway telescope with the walking end car. The models come with a control system with forward and reverse steering and grade control. It can be censored off string line or other methods from our sensor library. This provides ease of operation and accuracy while texturing and curing. The transverse tining undercarriage has 12 inches (305 mm) of hydraulic vertical height adjustment and is controlled using a sonic sensor, allowing the tining carriage to trace the slab elevation.

Side feeders
The modern range of high-powered twin-screw side feeders is matched to each production sized extruder, featuring a variety of feeding options for both powder premixes and liquid formulations. The feeder body and hopper are made from stainless steel and have an access door for cleaning and maintenance, also including a level probe as an option. Hopper size can be modified to fit the work area. Side Feeders are designed to feed a variety of materials like glass-fibers, powder additives, mineral fillers etc. Side feeders can also be used for depolarizing applications through side venting. The Side feeder height is adjustable within a range and is portable. Barrels and screws are of special tool-steel material and suitably surface treated for required applications.
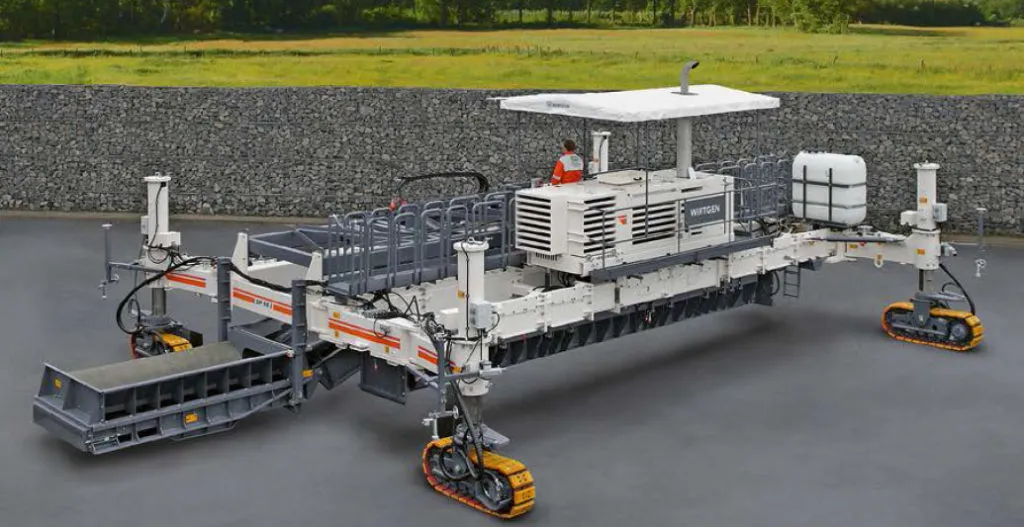
Placer/spreaders
Modern placer/spreaders are equipped with one conveyor and two auger drive circuits for placing and vibrator circuits for paving. There is a control system to unlock the incredible versatility of both a slip-form paver and a placer/ spreader, which quickly and efficiently interfaces with stringline or 3D machine guidance systems. The strike-off features independent vertical adjustment to control the placed concrete depth without raising and lowering the prime mover. The strike-off height is controlled by smart cylinders, independent of the prime mover, to meter the concrete ahead of the paver. Edge control and maximum material utilization are accomplished with pressure compensated side plates.

Image Source: wirtgen-group.com, volvoce.com, gomaco.com, apolloinffratech.com,