The method used to join the reinforcement bars, so that the force is transferred effectively from one bar to the other is called splicing. The method involves joining the bars together and overlapping them, but leaving at least two bar diameters between the bars.
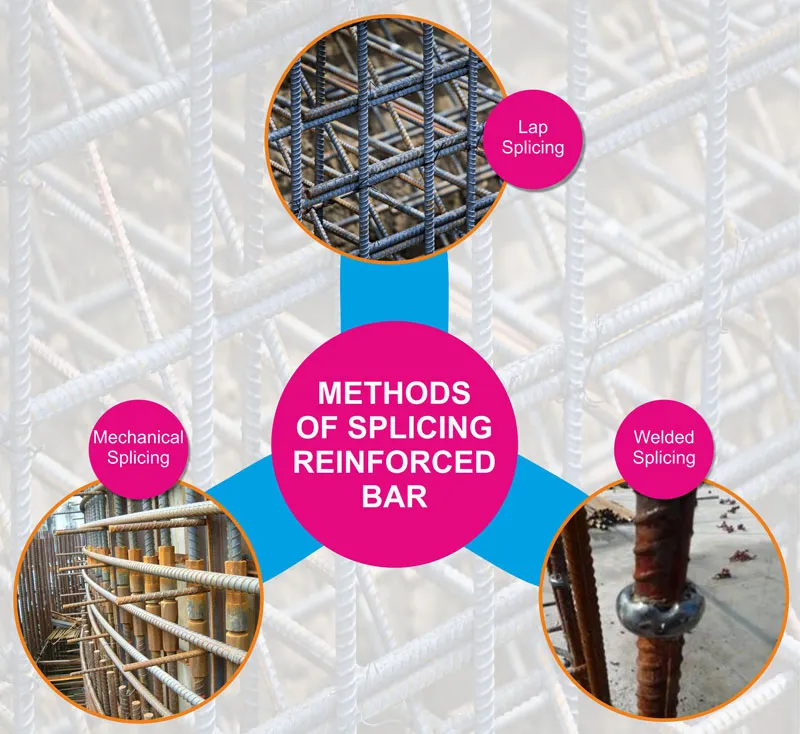
Different methods of Splicing Reinforced Bar
Lap Splicing
This type of splicing is done using a lap splice to join two pieces of rebar overlap to form a continuous reinforcement. This helps transfer loads properly throughout the structure. There are two types of lap splices: contact lap and non-contact lap splices. The lapped sections of contact lap splices are wired together. Lapped sections of non-contact lap splices do not touch and are permitted in practice provided the distance between lap sections meets the specified code requirements.
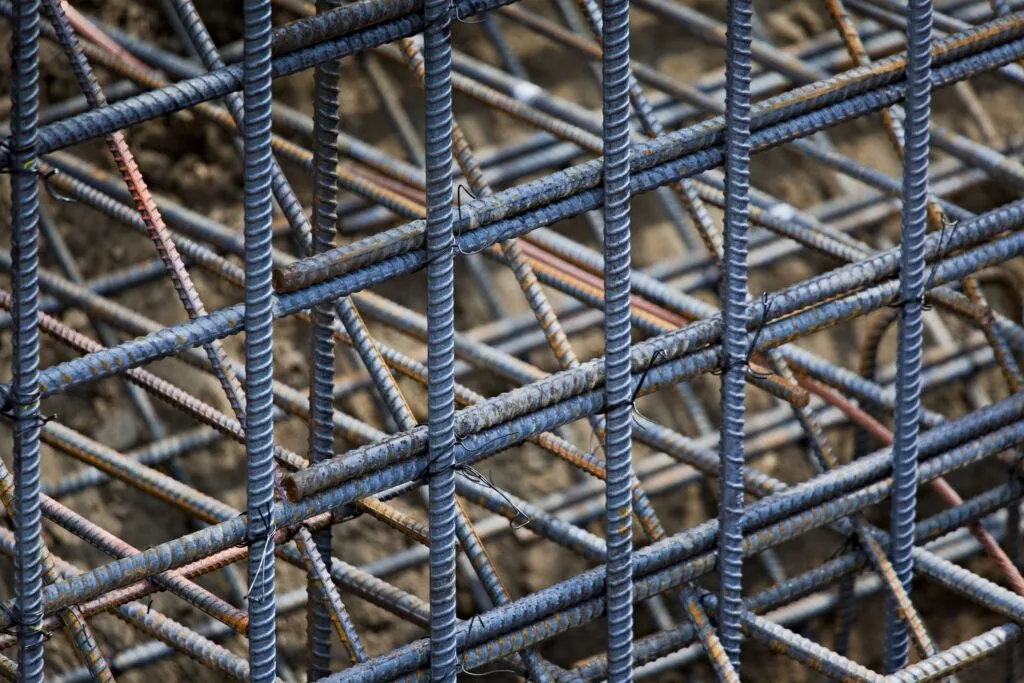
Mechanical splicing
In this method of splicing, the bars in direct contact are mechanically connected through sleeves or other similar devices. The method is used to create connections between two pieces of rebar that enable the bars to act like continuous lengths of rebar. Mechanical splices join rebar end-to-end, providing many of the advantages of a continuous piece of rebar. Mechanical splicing methods are being adopted in project sites due to their flexibility of use in congested reinforcement places at construction joints.
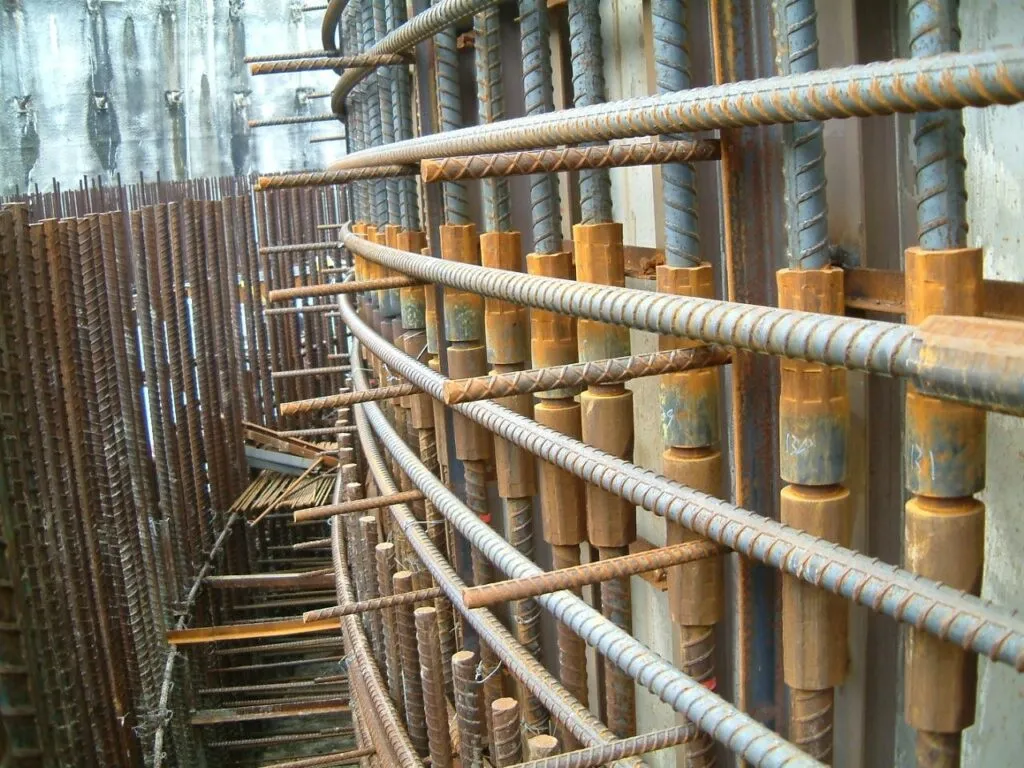
Welded splicing
This method of splicing is done by welding so that the stresses are transferred by weld. Welded splicing is used for special conditions splicing of rebars with a diameter greater than 36mm.
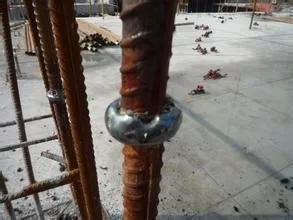
Conclusion
The need for a more efficient splicing system is becoming more apparent as a result of the increased construction complexities and design requirements.