The construction equipment market is again on fast track mode owing to the ambitious infrastructure creation plans and the new reforms in mining. There will be a growing requirement of aggregated equipment in the coming years to meet the demand from the construction and infrastructure sector. This recent trends anticipates an increased demand for crushers. In the construction sector, growth in roads, railways, irrigation, and other infra projects will drive the material processing equipment industry.
Factors such as government support to build infrastructure and increase in construction projects across India have fueled the growth of the market. Given below are a few models used across projects in India,
Pre-crushing of natural rock with customized jaw crusher
Newer jaw crusher models are more focused on safety and easy maintenance. Hydraulic separation and individual lifting of shells are in a trend that creates a better environment for any workers on-site working with the equipment. The size of a jaw crusher is designated by the rectangular or square opening at the top of the jaws. Primary jaw crushers are typical of the square opening design, and secondary jaw crushers are of the rectangular opening design. A Jaw Crusher reduces large size rocks or ore by placing the rock into compression. Due to their smaller physical size, jaw crushers are also ideal for tight spaces, such as underground mining and mobile crushing applications.
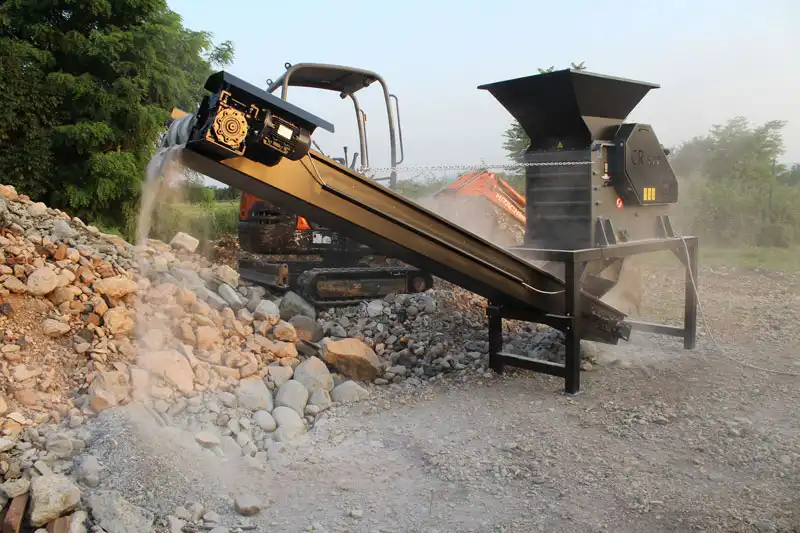
Crushers customized for shaping applications
The modern crusher range is ideal for shaping applications including making chips, sand, concrete manufacture, and glass recycling. The range includes both horizontal and vertical impact crushers. They are used as primary, secondary, or tertiary crushers depending on the Producer’s final-product-size needs. Impact Crushers are available in stationary, track, and portable configurations meeting any demand for any of these industries. The new hybrid models of impact crusher are engineered for maximum feed size, target output size, and total capacity. The newer models are capable of producing construction-grade aggregate, artificial sand and stone materials, run of mine material, especially for the secondary and tertiary crushing stages.

Crusher for the rigid surface to compress and break large rocks
The new crusher consists essentially of a long spindle, carrying a hard steel conical grinding element, the head, seated in an eccentric sleeve. The spindle is suspended from a “spider” and, as it rotates, normally between 85 and 150 rpm, it sweeps out a conical path within the fixed crushing chamber, or shell, due to the gyratory action of the eccentric. These crushers provide high throughput and less downtime to bring maximum efficiency to your operation. The new primary gyratory crushers have new advancements that bring increased speeds, higher installed power and mechanical improvements. All of these combine to bring additional throughput for your primary gyratory crusher.
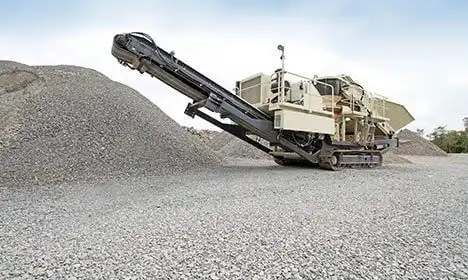
Crusher with ‘hammering rock’ configuration
New age vertical shaft impact crushers take full advantage of the so-called rock-on-rock crushing process. In vertical shaft impact crushers, the crushable material is fed through the centre of the rotor, where it is accelerated to high speed before being discharged through openings in the rotor periphery. The material is crushed as it hits the outer body at high speed and due to rocks colliding against each other. Vertical shaft impact crushers are generally utilized at the last stage of the crushing circuit, mostly in aggregate production and construction industry, but also preparing material feed for grinding mills in mining operations.
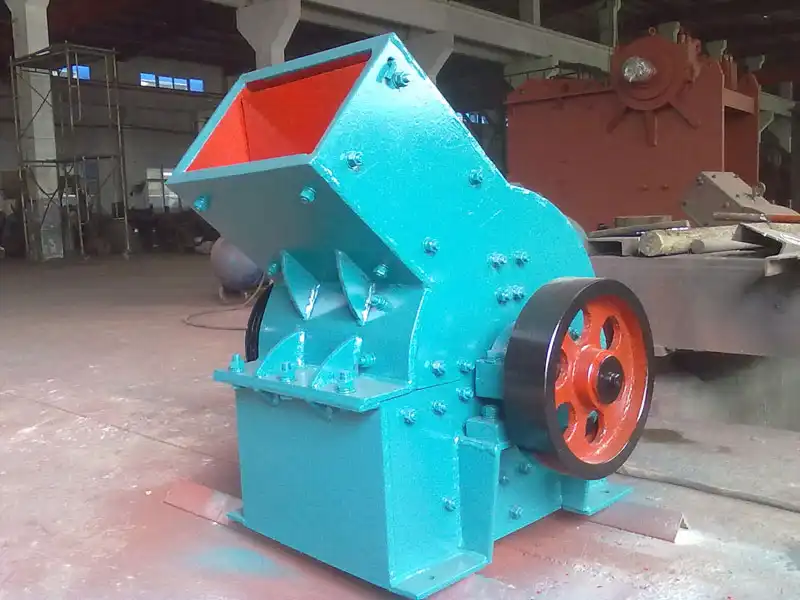
Crushers with multi-cylinder hydraulic cone systems
The new hybrid models of cone crusher come with multi-cylinder hydraulic cone systems suited for the secondary or tertiary stages of crushing plants by changing body liners and adaptors. It comes with the automatic control and fingertip manipulation system and two hydraulic cylinders that have a protective effect that if one overloads, then another one can fast react to clear choke merely by remote control. The crushed material is discharged at the bottom of the machine after they pass through the cavity. Cone crushers are popular rock crushing machines in aggregate production, mining operations, and recycling applications. They are normally used in secondary, tertiary, and quaternary crushing stages.
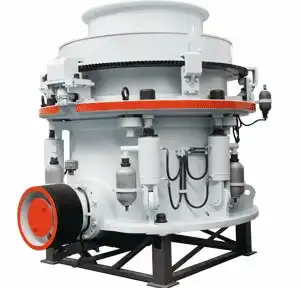
Tracked crusher for road construction work
The Diesel-Electric Tracked Crushers deliver higher productivity with a lower cost per tonne due to higher fuel efficiency & lower cost of maintenance. Modern models adopt self-drive mode, possess advanced technology, and complete function. Under any terrain condition, this equipment can get to anywhere in the workplace, in this way, it can decrease the operation to the material, besides, it is also convenient to comprehensively assist the coordination of mechanical equipment. With the control of a wireless remote, it is easy to place the crusher to trail car and transport to the operating site. Because it does not have to spend on assembly time, therefore the equipment can throw into work immediately when it arrives at the operating site. The newer models use a direct drive system for optimum fuel efficiency and low operating costs and include several user-friendly features. This ensures that they’re both simple to operate, and easy to maintain.
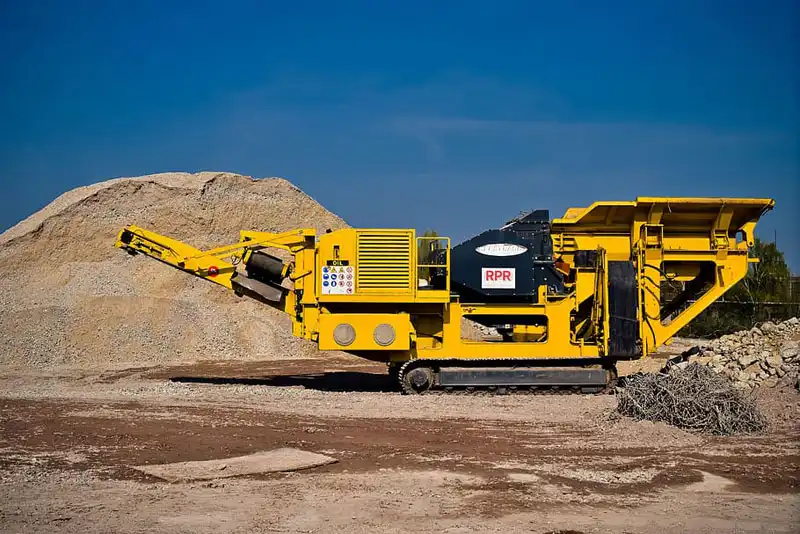
Conclusion
The newer crusher models of this generate high-quality aggregates, cubical in shape, with superior soundness. The newer models of this machine are driven by a motor with speed reducer and peripheral large gear, or a low-speed synchronous motor with peripheral large gear. Mobility and versatility have been key factors in the development of new models, with many firms also offering new options in the shape of electric and hybrid drive systems.
Image Source: directindustry.com, wirtgen-group.com, tenmat.com, ecvv.com, yecomachinery.com, pxfuel.com, miningreview.com