Ultra-high-performance concrete- UHPC is an advanced cementitious material with high strength and excellent durability. It offers the potential to become a practical solution to improve the sustainability of buildings and other infrastructure components. For the past two decades, UHPC is gaining increased interest in many countries with the usage ranging from building components, bridges, architectural features, repair and rehabilitation, vertical components such as windmills towers and utilities towers to oil and gas industry applications, off-shore structures, hydraulic structures and overlay materials.
UHPC is a relatively new generation of cementitious material with very high strength, ductility and durability. UHPC strengthened with fiber can be treated as a combination of three concrete technologies of self-compacting concrete (SCC), fiber reinforced concrete (FRC) and high-performance concrete (HPC). French interim recommendations (AFGC 2002) defined UHPC as a concrete with a characteristic compressive strength of at least 150 MPa with the use of steel fiber reinforcement to ensure ductile behavior under tension. UHPCs with compressive strength of 130 MPa – 150 MPa strengthened with either steel or other fibers are considered as lower strength UHPC. Normally, the term UHPC is used to describe a fiber reinforced, superplasticized, silica fume-cement mixture with a very low water to cement ratio (W/C), characterized by the presence of a very fine quartz sand that ranges from 0.15–0.60 mm in diameter, instead of the ordinary aggregate.
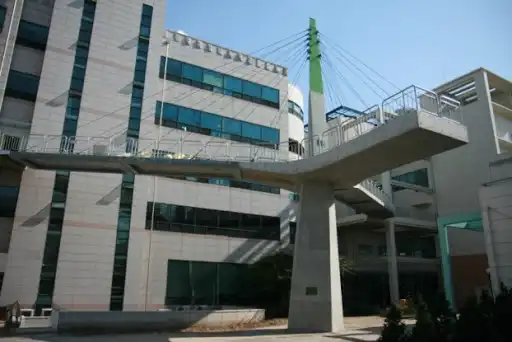
There are several types of UHPC that have been developed in different countries and by different manufacturers such as Ceracem®, BSI®, compact reinforced composites (CRC), multi-scale cement composite (MSCC), and reactive powder concrete (RPC). In Malaysia, UHPC started its industrial-commercial penetration as a sustainable construction material in late 2010 under the name Dura®.
UHPC has a compressive strength 10 times that of traditional concrete. Compressive strength is the ability of a material to resist bending under a load (or in compression). Normal concrete used in bridges has a compressive strength of 3,000 to 5,000 psi. UHPC has a compressive strength of 18,000 to 35,000 psi. Another measure of strength is tensile strength or tension. This is how strong a material is when you pull it. While traditional concrete has a tensile strength of 400 – 700 psi, UHPC has a tensile strength of about 1400 psi. Ultra-high performance concrete (UHPC) is a cementitious composite characterized by high compressive strength, typically greater than 120 MPa, specific durability, tensile ductility, and toughness.
In the basic composition of UHPC, the aggregate is a filler and the binder reacts with water to form a matrix with cementing ability and a lubricating effect. In addition to lubricating the aggregate particles and providing proper workability, the matrix must fully solidify the aggregate particles to ensure the engineering properties of the hardened concrete. Considering the high strength and durability requirements of UHPC, the packing density of the particles must be increased. To ensure the sufficient strength of UHPC, silica fume and ultra-fine silica powder are often used in the matrix composition to increase the packing density of the particle system, thereby increasing the strength of the matrix. In addition to supplementary cementitious materials, a thickening agent is added, as is a suitable amount of a superplasticizer to ensure the proper fluidity and viscosity of the prepared matrix. Fibers are blended to increase the tensile and spalling resistance of the matrix. Because UHPC has many advantages, its application has been increasing since the advent of its research and development.
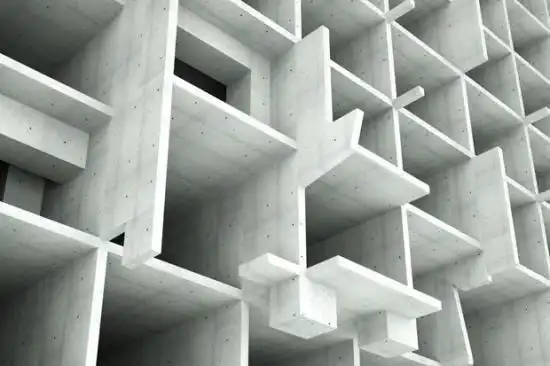
UHPC production principles
Over the past years of concrete remarkable advances, many researchers have developed UHPC up to a level where they are ready for applications. The compressive strength for the designed UHPC could reach up to 200 MPa. The basic idea of producing concrete with very high strength and dense microstructure had already been put forward in the 1980s. However, the practical breakthrough came after the development of efficient SP that enabled the production of easy flowing concrete with a high proportion of optimally packed ultrafine particles to minimize the composite porosity using extremely low W/B.
Several researchers have identified the basic principle in designing UHPC, which can be summarized as follows:
- Minimizing composite porosity by optimizing the granular mixture through a wide distribution of powder size classes and reducing the W/B.
- Enhancement of the microstructure by the post set heat treatment to speed up the pozzolanic reaction of SF and to increase mechanical properties.
- Improvement of homogeneity by eliminating coarse aggregate resulting in a decrease in the mechanical effects of heterogeneity.
- Increase in ductile behaviour by adding an adequate volume fraction of small steel fibers.
Application of the first four principles leads to concrete with a very high compressive strength and the addition of the steel fibers helps to improve both tensile strength and ductility of the concrete

Properties of UHPC
Compared with ordinary concrete, ultra-high performance concrete (UHPC) has excellent toughness and better impact resistance. Under high temperatures, the microstructure and mechanical properties of UHPC may seriously deteriorate. As such, we first explored the properties of UHPC with a designed 28-day compressive strength of 120 MPa or higher in the fresh mix phase, and measured its hardened mechanical properties at seven days. The test variables included: the type of cementing material and the mixing ratio (silica ash, ultra-fine silicon powder), the type of fiber (steel fiber, polypropylene fiber), and the fiber content. Its properties include –
- Ultra-high performance concrete (UHPC) is a modern composite material with extremely good mechanical characteristics.
- UHPC is more homogeneous than NSC due to optimized packing density and limited use of coarse aggregates. The size and strength difference between the matrix and the fine aggregates are so small that under external action
- UHPC displays ductile material behavior and its tensile performance can be significantly improved
- Nanomaterial in UHPC accelerates the hydration of cement, densifies the microstructure, improves strength, and thus contributes to its durability
- HPC matrix has very low permeability
- UHPC has a compressive strength 10 times that of traditional concrete. Compressive strength is the ability of a material to resist bending under a load (or in compression)
- The packing density of UHPC is optimized
- UHPC showed extremely low chloride migration when tested, less than 10% the permeability of normal concrete
- UHPC demonstrates excellent abrasion resistance, nearly twice as resistant as normal concrete
- UHPC has properties similar to hard rock
- UHPC typically is made with high-strength steel fibers, fine sand, cement, fly ash, a large volume of SF, and a low amount of water (a w/cm ratio less than 0.20).

UHPC materials
The materials within UHPC fall into three-component premixes: powders, superplasticizer, and organic fibers. The ingredients are:
- Portland cement
- Silica Fume
- Quartz flour
- Fine silica sand
- High-range water reducer
- Water
- Steel or organic fibers
Some manufacturers have created just-add-water UHPC pre-mixed products that are making UHPC products more accessible. The American Society for Testing and Materials has established ASTM C1856/1856M Standard Practice for Fabricating and Testing Specimens of Ultra High Performance Concrete that relies on current ASTM test methods with modifications to make it suitable for UHPC.

UHPC applications
The ultra-high performance concrete market is widely accepted in residential high-rise buildings, owing to various advantages offered, which include durability, high strength, and protection from extreme weather conditions. The growth of the ultra-high performance concrete (UHPC) market is largely associated with the growth in the residential applications in the construction industry. Its application areas includes-
- Prestressed girders
- Precast waffle panels for bridge decks
- Field-cast closure pours for prefabricated bridge elements (Joint-Fills)
- Precast concrete piles
- Seismic retrofits of bridges
- Thin bonded overlays of bridge decks
- Security and blast mitigation applications
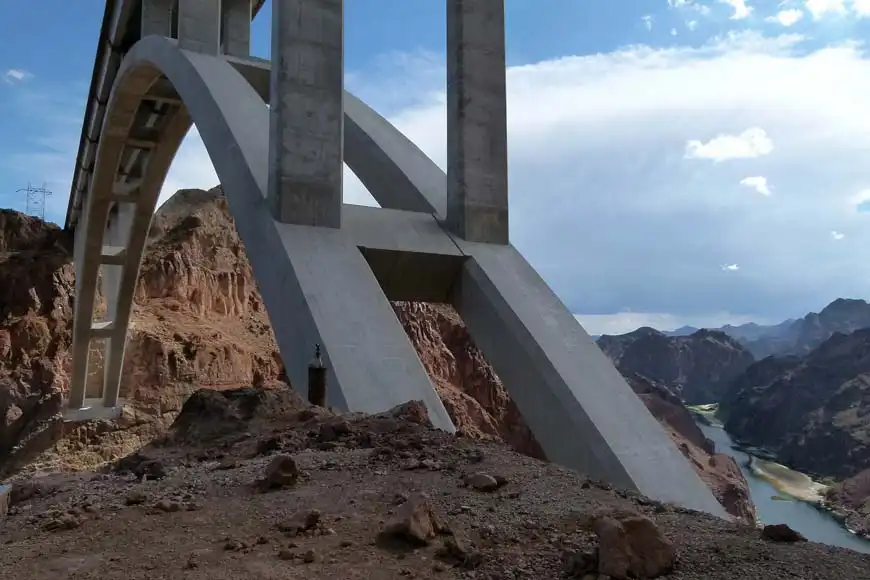
Conclusion
Cement production is the third highest source of CO2 emissions, behind automobiles and coal plants. UHPC represents exciting potential to dramatically reduce the environmental impact of cement production in construction by replacing 4 inches of precast traditional concrete with 5/8” of UHPC while at the same time affording a corresponding reduction in the weight of steel and other structural materials required for the foundation, core and shell of a building. Ultra High Performance Concrete (UHPC) is a material that is attracting attention in the construction industry due to the high mechanical strength and durability, leading to structures having low maintenance requirements. The construction industry is expected to push the concrete industry to new altitudes, which, in turn, will help the construction market achieve greater revenues and volumes in the near future, which will drive the demand for UHPC at a significant pace. Factors such as the increasing number of new housing units and huge investments in the infrastructural sector are expected to drive the UHPC market. Also, the increasing demand in China, Japan, Malaysia, South Korea, and other countries, due to the tremendous growth of construction opportunities in these countries, has also driven the market for UHPC.
References: sciencedirect.com, UPHC Solutions.com, cement.org, hindawi, market and markets.com, ed808.com, bridgetech-world.com, lafargeholcim.us, archello.com, walo.com, lactiowa.org, pdhstar.com