Admixture is added in concrete or mortar for increasing the rate of hydration of hydraulic cement and for shortening the setting time. Admixtures are added to the concrete batch immediately before or during mixing concrete. Concrete admixtures can improve concrete quality, manageability, acceleration, or retardation of setting time, among other properties that could be altered to get specific results.
Chemical admixtures help to reduce the cost of construction, modify properties of hardened concrete, ensure the quality of concrete during mixing/transporting/placing/curing, and overcome certain emergencies during concrete operations. Various types of admixtures are used in concrete to enhance the performance of concrete. Some of them are explained below.
Water Reducing Admixtures
Water reducing admixtures are special chemical products added to a concrete mixture before it is poured. They are from the same family of products as retarders. The essential materials used to produce normal water-reducing admixtures are the salts of lignosulphonate and hydroxycarboxylic acids. Less commonly modified carbohydrates (sometimes known as hydroxylated polymers) have formed the basis of a series of proprietary admixtures. Water reducing admixtures help in increasing the rate of gain of strength and increase workability. Water-reducing admixtures are used to obtain specific concrete strength using lower cement content. With this type of admixture, concrete properties are improved and help place concrete under difficult conditions.
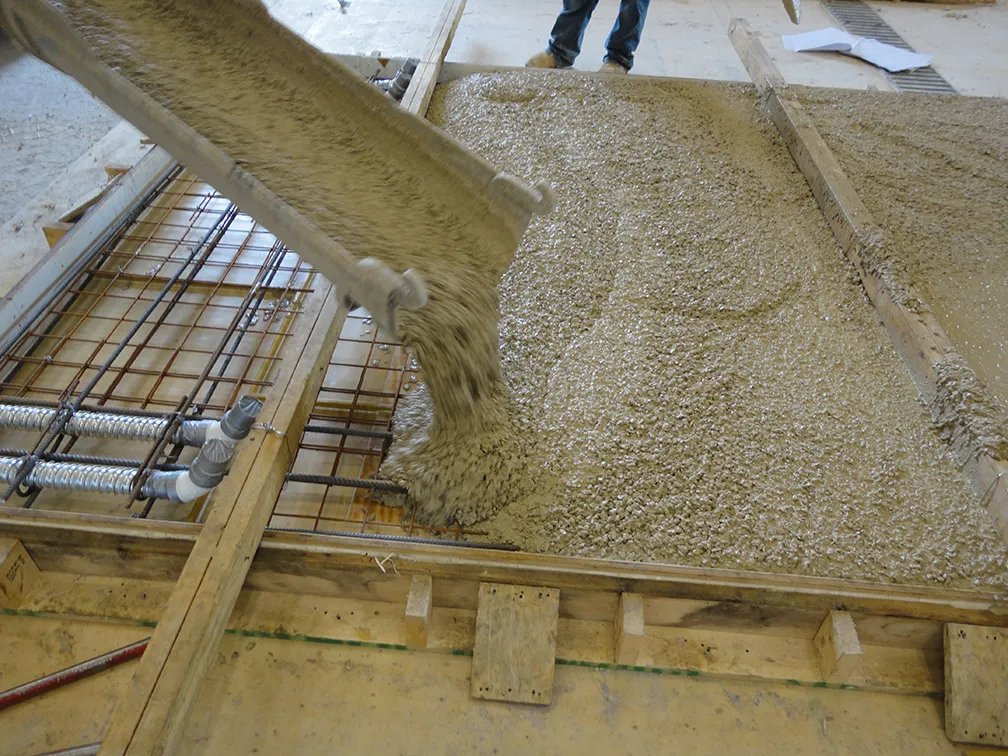
Retarding admixtures
Retarding admixtures (retarders) are known to delay hydration of cement without affecting the long-term mechanical properties. They are used in concrete to offset the effect of high temperatures, which decrease setting times, or to avoid complications when unavoidable delays between mixing and placing occur. Use of set retarders in concrete pavement construction enables farther hauling, thus eliminating the cost of relocating central mixing plants. It allows more time for texturing or plastic grooving of concrete pavements. It also allows more time for hand finishing around the headers at the start and end of the production day and helps eliminate cold joints in two-course paving and in the event of equipment breakdown. As with plasticisers, ultimate strength gain increases as water is reduced. Set retardation allows the slower formation of a more ordered, smaller, denser cementitious matrix. This increases ultimate strength relative to an unretarded mix with the same w/c ratio.
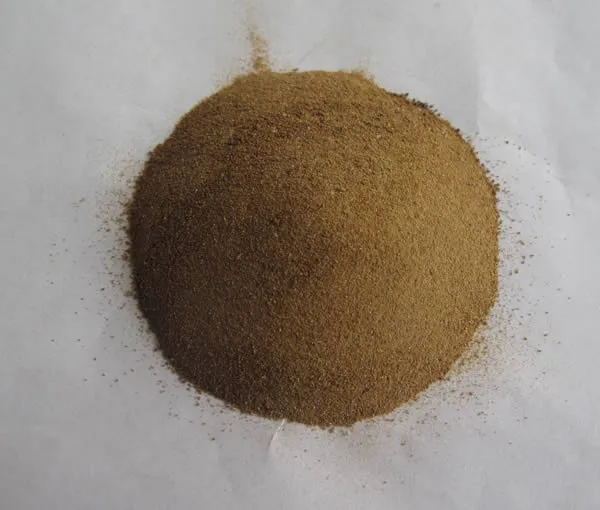
Accelerating admixtures
Accelerating admixtures are added to concrete to increase the rate of development of strength and to shorten the setting time. The compounds which can be used are Calcium chloride, calcium formate Triethanolamine (TEA), Soluble organic salts, Sodium nitrite, Sodium sulfate, Sodium aluminate, Sodium silicate, Sodium carbonate and Potassium hydroxide. Accelerating admixtures affect the rates of reactions between cement and water to give an overall increase in the hydration rate. Thus, the use of accelerators in concrete provides a shortening of setting time and/or an increase in early strength development. Accelerating admixtures can be used to increase either the rate of stiffening or setting of the concrete or the rate of hardening and early strength gain to allow earlier formwork striking and demoulding. Most accelerators achieve one rather than both of these functions. Hardening accelerators are most effective at low temperature. Accelerators can be used with superplasticizers where early age strength is required, especially at lower temperatures.
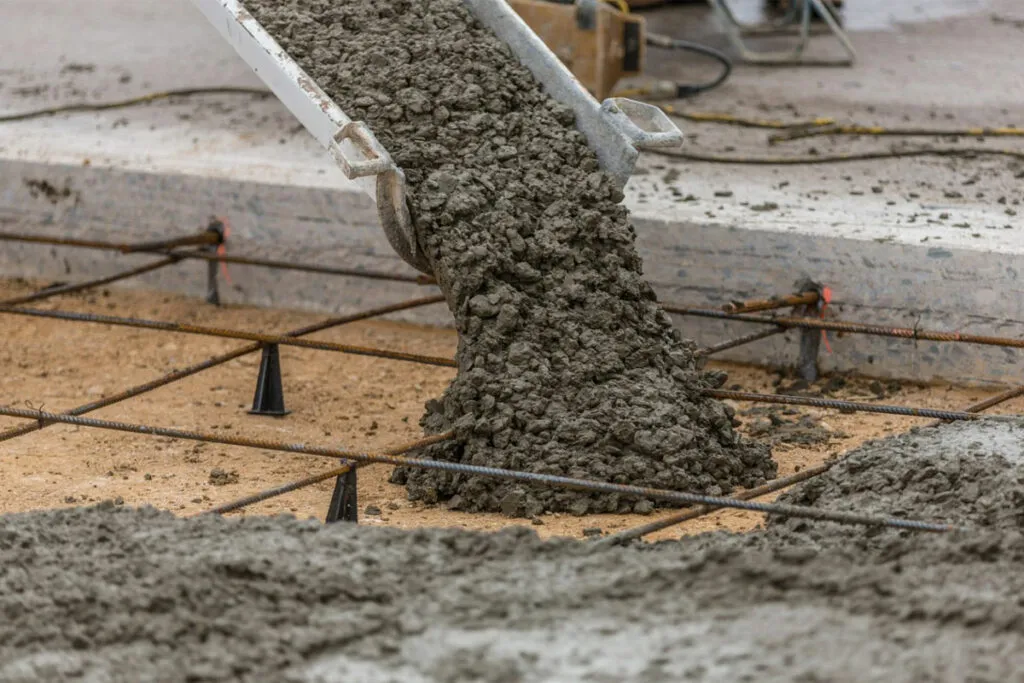
Air-entraining admixtures
Air-entraining admixtures is an admixture that causes the development of a system of microscopic air bubbles in cement paste during mixing, usually to increase its resistance to freezing and thawing and to improve workability It helps to incorporate a controlled amount of air, in the form of millions of minute non-coalescing bubbles distributed throughout the concrete, during mixing, without significantly altering the setting or rate of hardening of concrete. With the proper amount of entrained air, workability and durability of concrete is increased. The compounds which can be used are Natural wood resins, fats, lignosulfonates, alkyl sulphates. sodium salts of petroleum and sulphonic acids. Air entrainment is the intentional creation of tiny air bubbles in concrete. A concrete maker introduces the bubbles by adding to the mix an air entraining agent, a surfactant (surface-active substance, a type of chemical that includes detergents). The air bubbles are created during mixing of the plastic (easy flowing, not hardened) concrete, and most of them survive to be part of the hardened concrete. The primary purpose of air entrainment is to increase the durability of the hardened concrete, especially in climates subject to freeze-thaw; the secondary purpose is to increase workability of the concrete while in a plastic state in concrete.
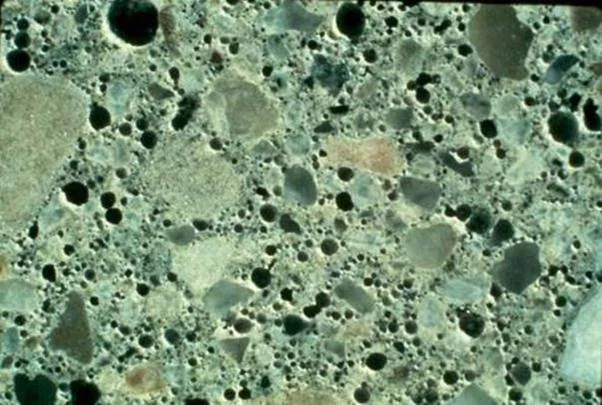
Pozzolanic Admixtures
Pozzolans are silicate-based materials that react with (consume) the calcium hydroxide generated by hydrating cement to form additional cementitious materials. The material is often used as admixture to prepare dense concrete mix which is suitable for water retaining structures like dams, reservoirs etc. They also reduce the heat of hydration and thermal shrinkage.The benefits of pozzolan use in cement and concrete are threefold. First is the economic gain obtained by replacing a substantial part of the Portland cement by cheaper natural pozzolans or industrial by-products. Second is the lowering of the blended cement environmental cost associated with the greenhouse gases emitted during Portland cement production. A third advantage is the increased durability of the end product. Blending of pozzolans with Portland cement is of limited interference in the conventional production process and offers the opportunity to convert waste (for example, fly ash) into durable construction materials.
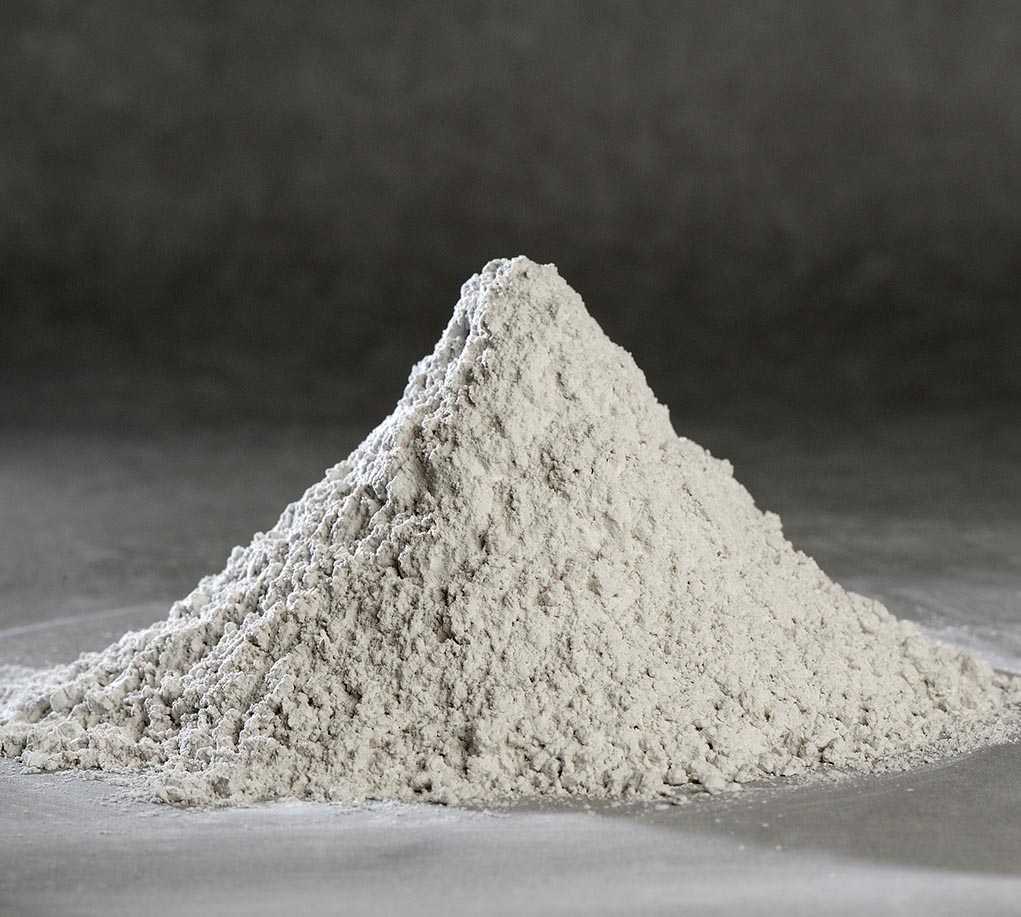
Waterproofing admixtures
Waterproofing admixture for concrete is also called as water resisting admixture and permeability reducing admixture. These admixtures prevent the passage of water through hardened concrete under a pressure head.There is a need for an admixture which can control the porosity of concrete.Waterproofing admixture Waterproofing admixtures are porous materials that have the ability to absorb water and water-borne contaminants. Hydrophobic and pore blocking ingredients react with products of the cement hydration process to produce a hydrophobic material which resists external water, decreasing absorption into the concrete. Waterproofing admixtures protect structures from degradation. They increase durability and reduce maintenance costs. Different types of admixtures are used for different parts of a structure namely the roof, basement or walls, as well as for different locations, climatic conditions, and purpose of the structure. Waterproofing admixtures have a broad range of applications in construction and infrastructure development.
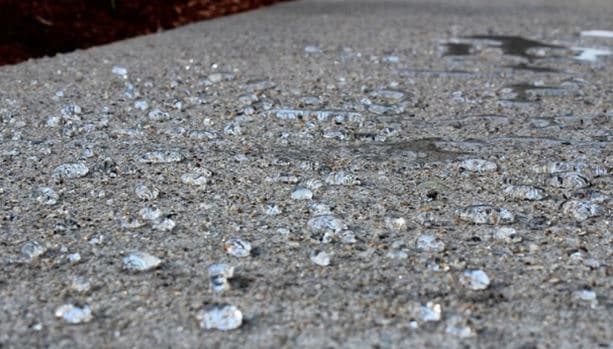
Gas–forming admixtures
Gas-forming admixtures help maintain concrete’s initial volume, counteracting settlement and bleeding, by generating or liberating bubbles in the mix. At higher volumes, these admixtures—generally consisting of hydrogen peroxide, aluminum powder, or activated carbon—can be used to make lightweight concrete. Aluminum powder, activated carbon, hydrogen peroxide are generally used gas forming chemical admixtures. When gas forming admixtures are added, it reacts with hydroxide obtained by the hydration of cement and forms minute bubbles of hydrogen gas in the concrete.For settlement and bleeding resistance purpose, a small quantity of gas forming admixtures which is generally 0.5 to 2% by weight of cement is used. But for making lightweight concrete larger quantities generally 100 grams per bag of cement is recommended.
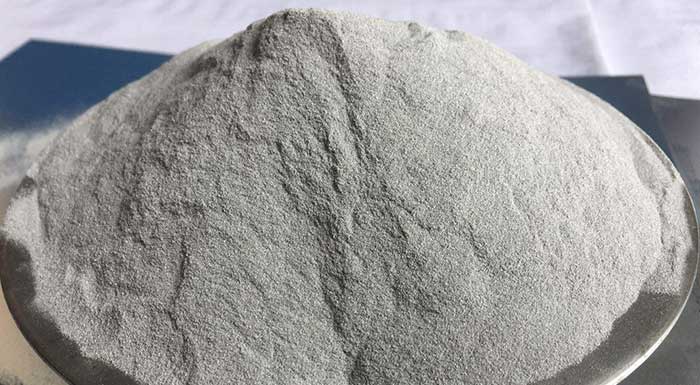
Air-detraining admixtures
Air-detraining admixtures destabilize air in fresh concrete, allowing it to escape during mixing, thus reducing the air content. Over-entrainment of air can be caused by inadvertently adding double dosages of admixtures or by using more than one admixture, both of which entrain some air. Some aggregates have been known to release air into the mix. The most widely used air-detrainer is tributyl phosphate. Dibutyl phosphate, water-insoluble alcohols, water-insoluble esters of carbonic and boric acids as well as silicones may also do the job. Obviously they must be used judiciously for the concrete to end up with the right amount of air. Tributyl phosphate, silicones, water insoluble alcohols are the most used air-detraining admixtures.
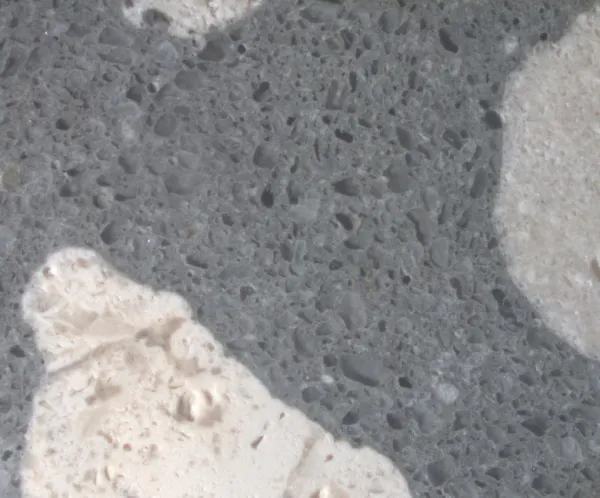
Alkali Aggregate Expansion Preventing Admixtures
In most concrete, aggregates are more or less chemically inert. However, some aggregates react with the alkali hydroxides in concrete, causing expansion and cracking over a period of many years. This alkali-aggregate reaction has two forms: alkali-silica reaction (ASR) and alkali-carbonate reaction (ACR). Alkali-silica reaction can be controlled using certain supplementary cementitious materials. In-proper proportions, silica fume, fly ash, and ground granulated blast-furnace slag have significantly reduced or eliminated expansion due to alkali-silica reactivity. ACR is relatively rare because aggregates susceptible to this phenomenon are less common and are usually unsuitable for use in concrete for other reasons. Aggregates susceptible to ACR tend to have a characteristic texture that can be identified by petrographers. Unlike alkali carbonate reaction, the use of supplementary cementing materials does not prevent deleterious expansion due to ACR. It is recommended that ACR susceptible aggregates not be used in concrete.
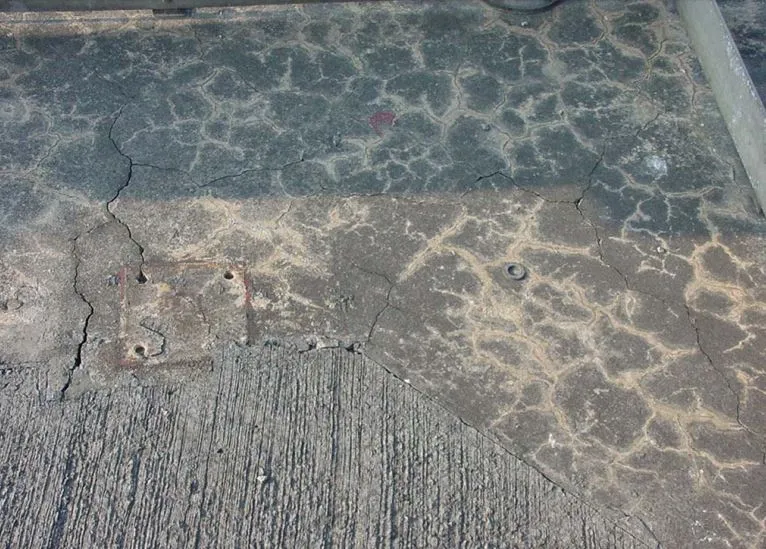
Anti-washout admixtures
Anti-washout admixtures concrete offers superior performance when the concrete is in a fresh state. By adding an anti-washout admixture to concrete and its viscosity is increased, There are a variety of types of anti-washout admixtures, such as those based on the cellulose system and the acrylic system. Also, the degree of anti-washout property and flow property differs depending on the brand of anti-washout admixture, even though the main Ingredient may be the same.
It is thus important to comprehend the performance of the anti-washout admixture to be used using available reference materials, as well as to confirm that the required quality can be obtained by conducting tests in advance using the chosen materials. The Antiwashout admixture is also called viscosity improving admixture, and it is occasionally employed to create self compacting concrete.
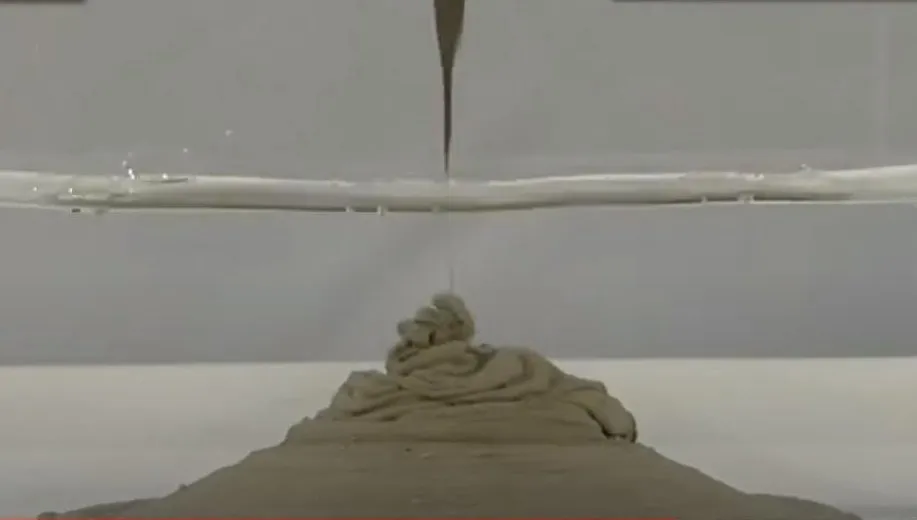
Grouting Admixtures
Grouting Admixture is a grouting mix for concrete as well as cement mortars. This admixture is used for the grouting of non shrink concrete, cement slurries and mortars. This is a free flowing grey powder that has specifically been made for the injection grouting of permeable concrete in structural restoration works as well as cable duct grouting of post tensioned bridge girders. It is also utilized for the infill mortars in sealing and filling the sealing, recesses, cut outs and foundation pockets. Accelerators like calcium chloride, triethanolamine etc. are used as grout admixtures when the grout is to be set rapidly. Similarly retarders like mucic acid, gypsum etc. are used to slow down the setting time of grout.
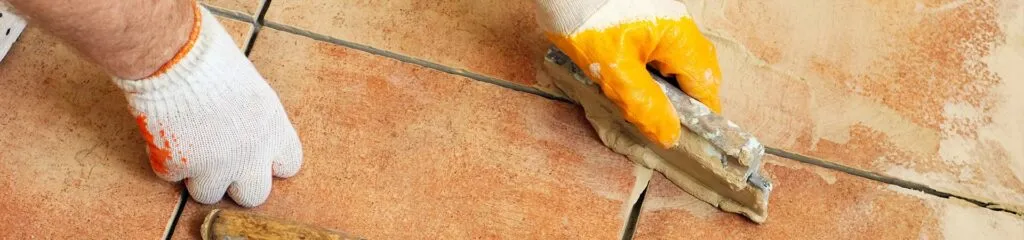
Corrosion inhibiting admixtures
Corrosion inhibiting admixtures increases the passivation of reinforcement and other embedded steel. This can inhibit corrosion when passivation would otherwise have been lost as a result of chloride ingress or carbonation. They are added to concrete during production and are referred to as ‘integral’ corrosion-inhibitors. So-called ‘migratory corrosion-inhibitors’ applied to hardened concrete are not admixtures. Corrosion-inhibiting admixtures have little effect on strength at either early or later ages. The function of this type of admixture is to enhance the long term durability of reinforced concrete by enhancing passivation to the cathodic and/or anodic areas of embedded steel.
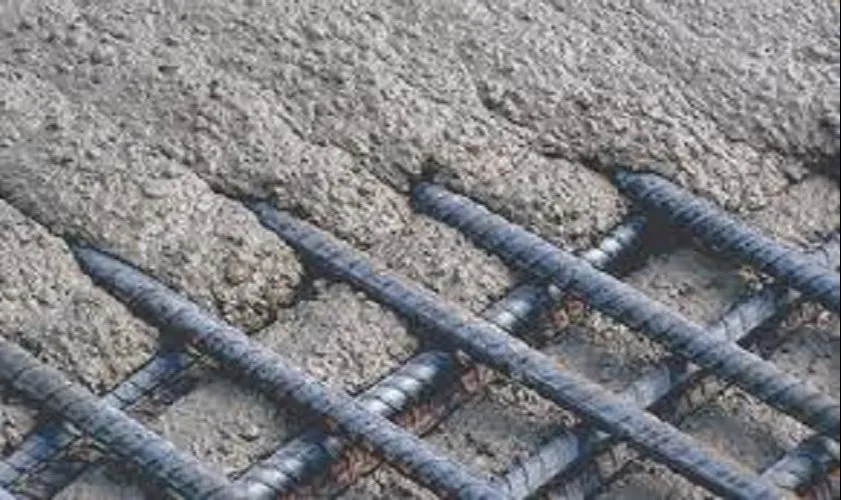
Bonding admixtures
Bonding admixtures significantly improve adhesion and cohesion as well as tensile, compressive, flexural and mechanical properties of cement based mixtures. This admixture will never re-emulsify when exposed to water. It will also improve freeze/thaw stability of Portland cement based products. These types of admixtures are used for pavement overlays, screed over roof provision and repair works. Bonding admixtures comprises Polyvinyl chloride, polyvinyl acetate, acrylics, butadiene-styrene co-polymers.
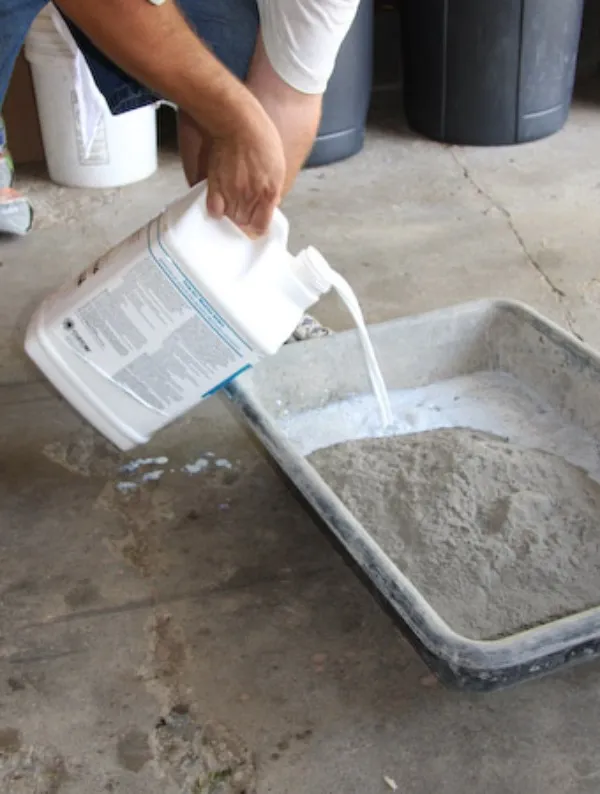
Fungicidal, Germicidal and Insecticidal admixtures
A plurality of microbicide agents that can be used alone or combined to avoid microbe adhesion and spreading at homes and several industry surfaces has been developed. These microbicide agents can be mixed for example with cleaning products, compositions and disinfectants, or being applied as wall coverings on fabrics, paper, adhesive strips, plastic materials sheets. Admixtures in Concretelists three materials which, when added in amounts in the range of 0.1 to 10 percent by weight of cement, inhibit the growth of fungi and bacteria- polyhalogenated phenols, dieldrin emulsion and copper compounds.
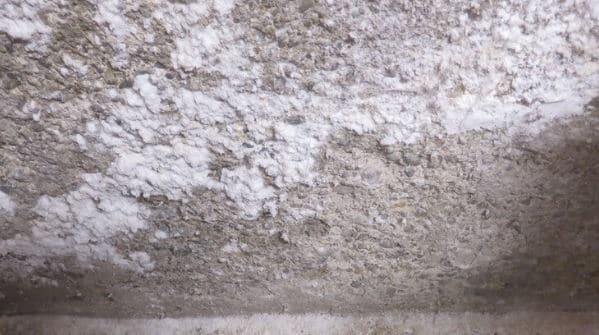
Coloring admixtures
Coloring admixtures infuse concrete with rich, long-lasting, fade-resistant color. Stamped concrete contractors often use this coloring medium to produce a backdrop for contrasting accent or antiquing colors, such as pigmented release agents and stains or dyes. This layering of color is what enables them to so closely replicate the variegated, multi-tonal appearance of natural stone.
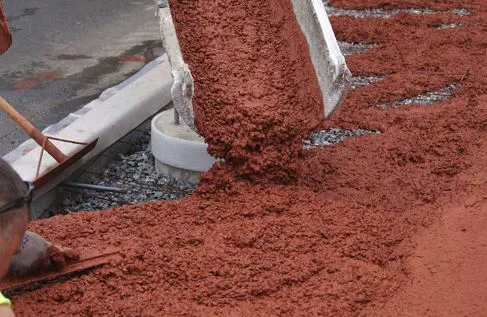
Conclusion
Every admixture has its one individualistic properties and material composition. It is very important to know the applicability of each one before using them. It is suggested to take expert opinion when selecting them. The cost of these admixtures will vary depending on the quantity and type of admixture being used. All of this will be added to the cubic yard/meter cost of concrete.